Glencore Merafe’s Tswelopele project lauded for slashing energy use by 21%
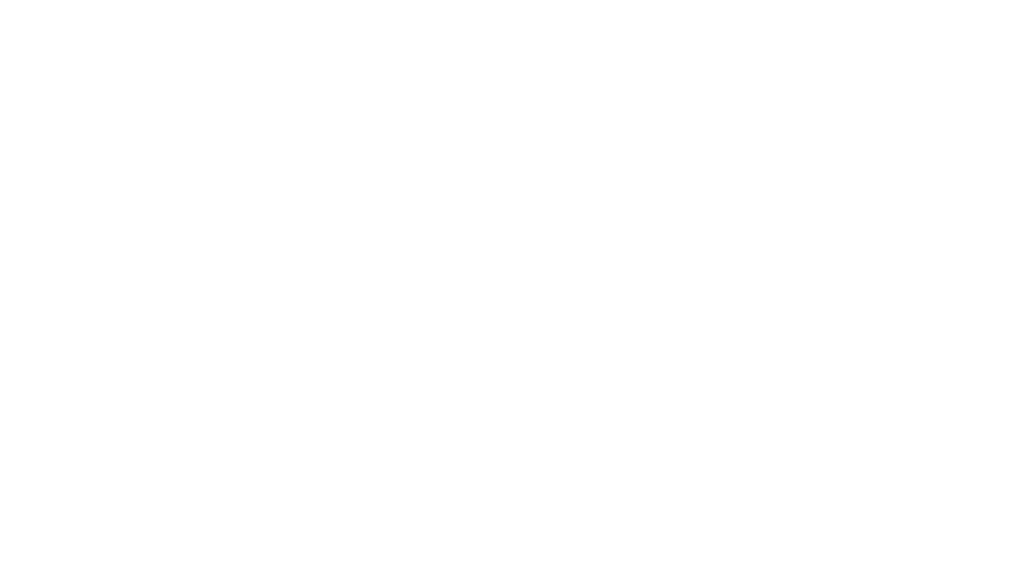
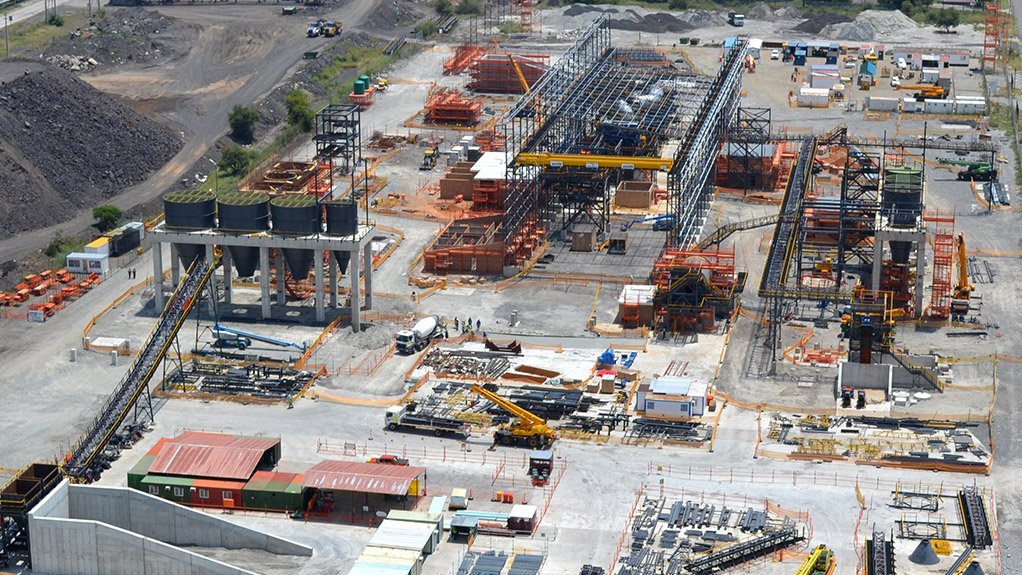
TSWELOPELE PELLETISING AND SINTERING PLANT The Tswelopele project started in 2010 and was aimed at developing a 600 000 t/y chrome-fines pelletising and sintering plant at its Rustenburg operation
The implementation of chrome venture Glencore Merafe PSV’s R800-million Tswelopele project, undertaken at the venture’s Rustenburg ferrochrome smelting complex, saw it reduce its energy use by 21.3% in 2011/12 compared with the same period in 2013, which translates into a yearly saving of about 150 711 MWh.
This achievement was recognised and rewarded when the venture’s Tswelopele project was announced the joint winner with steelmaker ArcelorMittal South Africa’s Saldanha Works plant in the industrial category at the Eskom-sponsored Eta Awards ceremony held in December.
Following the lauding of its energy effi- ciency efforts by the State-owned power utility, Glencore Merafe PSV project team leader Dr Jurg Zaayman tells Mining Weekly that by using a technology to pelletise and sinter chrome-ore fines at the previously significantly energy-intensive Rustenburg complex, the company has succeeded in treating the ore to make the furnaces at the complex more energy efficient.
The Tswelopele initiative forms part of a capital investment programme that was started by Glencore Merafe PSV about ten years ago to improve the efficiencies of its furnaces. Since the start of the capital investment programme, the venture has spent about R6.7-billion on smelter expansions and about R1.6-billion on improving the efficiencies of its current smelting operations.
As a result of the decade-long investment, electrical energy efficiency has improved by more than 25% throughout the group.
The Tswelopele project started in 2010 and was aimed at developing a 600 000 t/y chrome-fines pelletising and sintering plant at its Rustenburg operation. The Tswelopele energy-saving initiative “saved” the previously energy intensive smelting complex, says Zaayman.
The Tswelopele pelletising and sintering plant, which employs about 100 people, processes fine ore from mines by grinding the ore in a ball mill to form a slurry. Filter cake is filtered from the slurry with ceramic filters and then mixed with a binding agent and pelletised in a drum into uniform pellets.
“The pellets are then sintered at 1 400 ºC in an energy efficient sinter furnace, in which the circulated air is used to cool down the pellets, while also used to preheat the air.
“While being sintered, the mineral structure of ore is broken to assist with the chemical reduction of the pellet to ferrochrome. This enables better permeability for easy gas flow in the furnace and also improves the furnace stability,” explains Zaayman.
The process presents a number of environmental advantages, such as reduced dust, reduced slag production and zero effluent production.
Another benefit of the energy efficient technology is its ability to use upper group 2 (UG2) chrome ore to make pellets and to use all the UG2 pellets in the furnace mix.
Further, the technology used at the Tswelopele pelletising and sintering plant ensures that less ore is used to make the same amount of ferrochrome. “In the past, the smelter consumed more ore for every 1 t of ferrochrome produced but has since been able to improve this by 30%,” says Zaayman.
The venture’s current furnace fleet consists of 22 furnaces – 20 existing furnaces and two that are being built. In the fleet, 13 furnaces are conventional semi-closed furnaces.
Zaayman notes that the Tswelopele pelletising and sintering plant exceeded its design capacity after its fourth month of operation, in January 2013, since it was hot-commissioned in October 2012.
The Tswelopele project created 600 contractor jobs during the construction phase and was able to preserve about 4 700 direct and indirect jobs (when using a multiplier of seven for the chrome industry).
The project team consisted of Zaayman and five other core members, including a project manager, a mechanical expert, two instrumentation experts and a project engineer.
Comments
Press Office
Announcements
What's On
Subscribe to improve your user experience...
Option 1 (equivalent of R125 a month):
Receive a weekly copy of Creamer Media's Engineering News & Mining Weekly magazine
(print copy for those in South Africa and e-magazine for those outside of South Africa)
Receive daily email newsletters
Access to full search results
Access archive of magazine back copies
Access to Projects in Progress
Access to ONE Research Report of your choice in PDF format
Option 2 (equivalent of R375 a month):
All benefits from Option 1
PLUS
Access to Creamer Media's Research Channel Africa for ALL Research Reports, in PDF format, on various industrial and mining sectors
including Electricity; Water; Energy Transition; Hydrogen; Roads, Rail and Ports; Coal; Gold; Platinum; Battery Metals; etc.
Already a subscriber?
Forgotten your password?
Receive weekly copy of Creamer Media's Engineering News & Mining Weekly magazine (print copy for those in South Africa and e-magazine for those outside of South Africa)
➕
Recieve daily email newsletters
➕
Access to full search results
➕
Access archive of magazine back copies
➕
Access to Projects in Progress
➕
Access to ONE Research Report of your choice in PDF format
RESEARCH CHANNEL AFRICA
R4500 (equivalent of R375 a month)
SUBSCRIBEAll benefits from Option 1
➕
Access to Creamer Media's Research Channel Africa for ALL Research Reports on various industrial and mining sectors, in PDF format, including on:
Electricity
➕
Water
➕
Energy Transition
➕
Hydrogen
➕
Roads, Rail and Ports
➕
Coal
➕
Gold
➕
Platinum
➕
Battery Metals
➕
etc.
Receive all benefits from Option 1 or Option 2 delivered to numerous people at your company
➕
Multiple User names and Passwords for simultaneous log-ins
➕
Intranet integration access to all in your organisation