Solution simplifies ore sorting
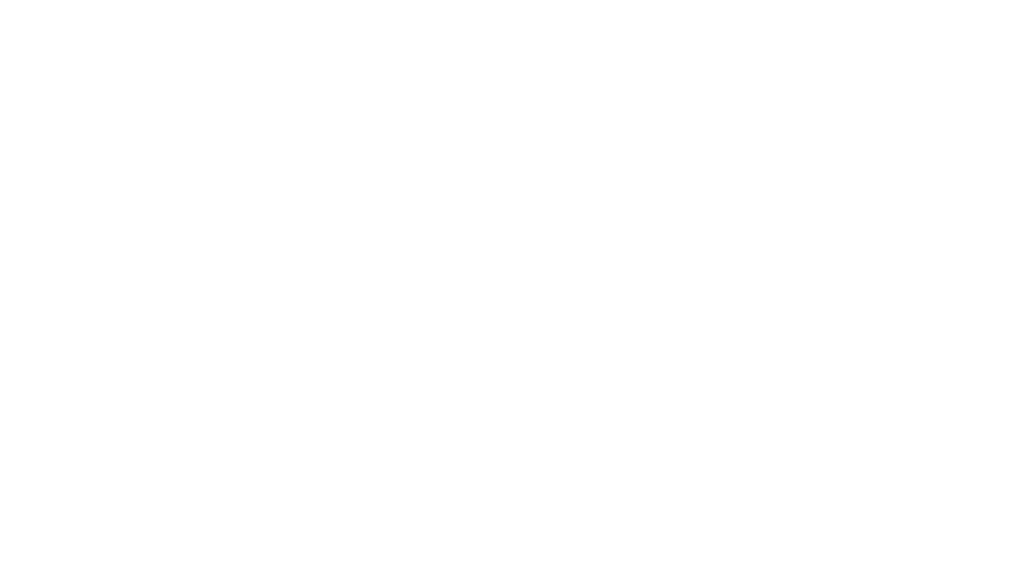
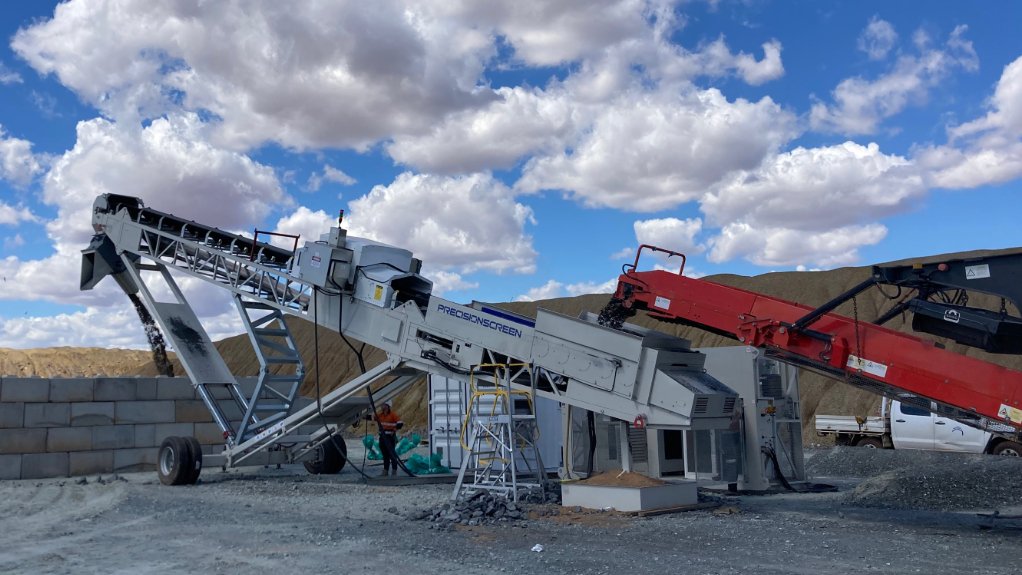
PRECISION GRADING NextOre's magnetic resonance analyser bulk ore sorting solutions are available as a mobile turnkey solution as well as being able to be fitted to the main feed conveyor
Increased metal recovery, reduced waste, improved water conservation and lower energy consumption can be achieved using original-equipment manufacturer NextOre’s advanced sensor system Magnetic Resonance Technology for large-scale ore sorting, which removes reject material prior to processing, reports NextOre sales head Rod Tayler.
Established in 2017, NextOre was co-founded by scientific research agency Commonwealth Scientific and Industrial Research Organisation (CSIRO), advisory and investor firm RFC Ambrian and engineering consultancy Worley.
NextOre manufactures and implements advanced sensor technology for the mining industry to unlock the full economic value of ore bodies while reducing environmental impacts, he explains.
“Our technology improves mining efficiency and helps tackle declining ore grades by making sure no metal is left behind and reducing the waste, maximising the economic value of that body,” he says.
Integrating its Magnetic Resonance Technology, NextOre provides two bulk ore sorting solutions, which include the magnetic resonance analyser (MRA) being fitted to the main feed conveyor and a mobile turnkey solution incorporating an MRA, conveyor with a pneumatic diverter.
Based on medical magnetic resonance imaging (MRI) technology, MRA was developed by CSIRO, in Australia.
The MRA enables real-time measurement of ore pods or parcels, automating the process of separating high-grade ore from low grade and rejecting through a diverter. This process increases ore head grade, extends mine life, enhances metal production and reduces processing costs, details Tayler.
He elaborates that the MRA offers precision ore grading in copper within two to four seconds, achieving potential feed rates of up to 12 000 t/h, and is able to cope with large variations in feed particle size.
Further, the MRA solutions do not require ongoing calibration checks, delivering consistent operational availability without any production interruptions, adds Tayler.
He elaborates that the MRA relies on safe very high frequency (VHF) radio frequencies as opposed to radiation-based alternatives, which have significant occupational health and safety requirements, and are restricted in some regions.
Additionally, an MRA facilitates higher ore recovery by identifying valuable ore within pit shells that might otherwise be discarded, creating significant potential fiscal gains without increasing mining equipment scale, thereby maintaining lowest possible cost a tonne.
NextOre’s technology is mineral-specific as the technology is only able to sense and report on ore grade that is visible to the MRA.
“The mineralogy of copper is such that the orebody will have a dominant mineral, such as chalcopyrite, that is highly sensing to the VHF frequency that the MRA produces. This allows us to effectively grade and bulk ore sort such minerals,” says Tayler.
Expansion in Africa
NextOre’s MRA technology has demonstrated success across several global mine sites, such as copper miner First Quantum Minerals’ Kansanshi mine in Zambia, which is now the largest on-conveyor ore sorter in the world. Pilot trials were also conducted at copper miner Capstone Mining’s Cozamin mine, in Mexico.
Tayler enthuses that each site has reported measurable improvements in copper production and ore grade, with the Cozamin mine achieving a 7.5% increase in copper production without additional mining.
Comments
Press Office
Announcements
What's On
Subscribe to improve your user experience...
Option 1 (equivalent of R125 a month):
Receive a weekly copy of Creamer Media's Engineering News & Mining Weekly magazine
(print copy for those in South Africa and e-magazine for those outside of South Africa)
Receive daily email newsletters
Access to full search results
Access archive of magazine back copies
Access to Projects in Progress
Access to ONE Research Report of your choice in PDF format
Option 2 (equivalent of R375 a month):
All benefits from Option 1
PLUS
Access to Creamer Media's Research Channel Africa for ALL Research Reports, in PDF format, on various industrial and mining sectors
including Electricity; Water; Energy Transition; Hydrogen; Roads, Rail and Ports; Coal; Gold; Platinum; Battery Metals; etc.
Already a subscriber?
Forgotten your password?
Receive weekly copy of Creamer Media's Engineering News & Mining Weekly magazine (print copy for those in South Africa and e-magazine for those outside of South Africa)
➕
Recieve daily email newsletters
➕
Access to full search results
➕
Access archive of magazine back copies
➕
Access to Projects in Progress
➕
Access to ONE Research Report of your choice in PDF format
RESEARCH CHANNEL AFRICA
R4500 (equivalent of R375 a month)
SUBSCRIBEAll benefits from Option 1
➕
Access to Creamer Media's Research Channel Africa for ALL Research Reports on various industrial and mining sectors, in PDF format, including on:
Electricity
➕
Water
➕
Energy Transition
➕
Hydrogen
➕
Roads, Rail and Ports
➕
Coal
➕
Gold
➕
Platinum
➕
Battery Metals
➕
etc.
Receive all benefits from Option 1 or Option 2 delivered to numerous people at your company
➕
Multiple User names and Passwords for simultaneous log-ins
➕
Intranet integration access to all in your organisation