South Africa on verge of nice breakthroughs in hydrogen, says new SAIMM president
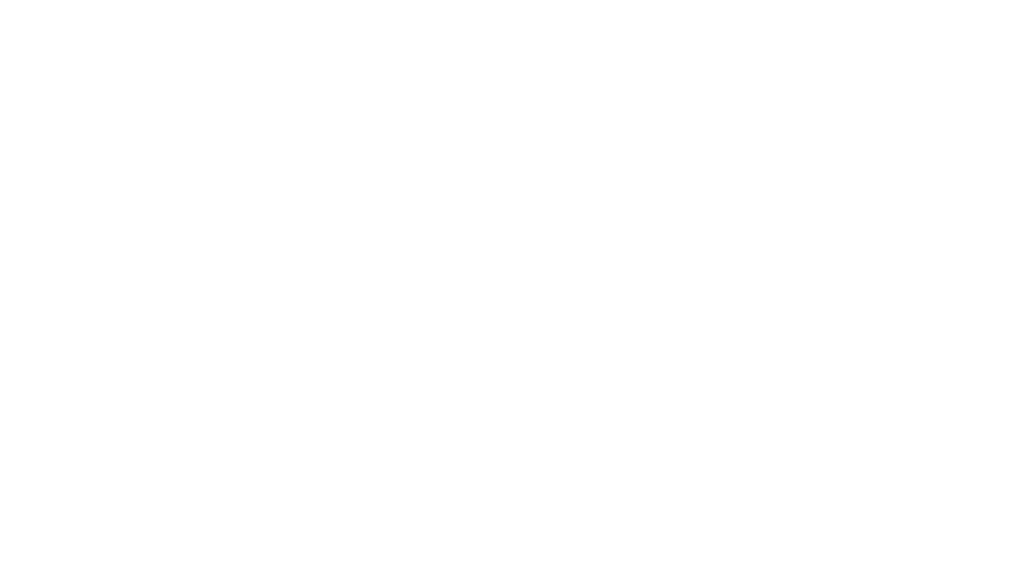
South African Institute of Mining and Metallurgy president Isabel Geldenhuys interviewed by Mining Weekly’s Martin Creamer. Video: Darlene Creamer.
JOHANNESBURG (miningweekly.com) – South Africa is on the verge of nice breakthroughs in hydrogen, says newly elected Southern African Institute of Mining and Metallurgy (SAIMM) president Isabel Geldenhuys.
Speaking to Mining Weekly in a Zoom interview, Geldenhuys expressed the view that all the big mines with big moving machinery will have the opportunity to move away from diesel and switch to a hydrogen-based fuel system because of the contained ecosystem. (Also watch attached Creamer Media video.)
While the use of green hydrogen is always first prize, Geldenhuys pointed out that many processes have grey hydrogen as a byproduct and expressed the view that where grey hydrogen is at the ready, it should be used as an imperfect solution rather than being left to go to waste.
She said that South Africa had the required hydrogen know-how as a consequence of the Department of Science and Innovation having supported the hydrogen economy concept for nearly 20 years.
“What really excites me is the focus on being greener and more efficient," Geldenhuys said.
On the multidisciplinary front, she said: "There are many opportunities for us to work together and bring interesting, transdisciplinary thinking into metallurgy to solve our big problems.”
Under her leadership, the SAIMM plans to strengthen its online presence so that it can communicate optimally with the rest of the mining and metallurgy world at a time of rising mining fortunes.
South Africa’s mining and metallurgy history extends across more than a century, which has resulted in a wealth of knowledge being accessible from SAIMM’s databases.
Geldenhuys, a former manager of Mintek's pyrometallurgy division, who is now a consultant, expressed excitement at renewable energy’s integration into smelting and the belief that “the stars are aligning” for the smaller mining companies when it comes to smelting.
She also highlighted the opportunity to use furnace off gases to recover heat, particularly when it comes to bulk commodities.
And where slag is a big byproduct, as is the case in the platinum group metals (PGMs) industry – where substantial slag byproduct emerges molten at 1 500 oC to 1 600 oC – the next envisaged step is to find a way to extract some of that waste heat from the slag.
“My vision for the year is to embed all the hard work we’ve been doing over the last five years in terms of reviving the interest in collaborating at technical conferences and sharing of knowledge.
“We have embarked on a process of identifying what it is that makes SAIMM invaluable to our members and we’re starting to communicate that message a lot clearer, and one of my big plans for the year is to work a lot on communicating to our members what we are offering them.
“Sharing of this knowledge is a big passion of mine,” said Geldenhuys.
Mining Weekly: How can the world make pyrometallurgy and smelting less energy intensive and more environment friendly?
Geldenhuys: I always say that Nature gave us minerals in a certain format, which requires energy. There is nothing you can do about it. For example, if we look at the ferrochrome industry, we can dream of making that a green industry by using hydrogen to reduce the chrome but there are certain requirements. We have to take something up to really high temperature, we have to give it some carbon for it to react. Now stainless steel and steel make the world go round. So how do they look at this problem differently? We say, yes, we need energy, but it doesn’t mean it has to be fossil fuel energy. There are lots of things we can do. It doesn’t mean that if we produce carbon dioxide (CO2) that you should let it go into the atmosphere. So where we look is at renewable energy and running a furnace with it. But it’s actually way more exciting than that. We have been working in pyrometallurgy on direct heat, using the heat from the sun in a concentrated mode to dry and to clean. The other exciting area is that a lot of processes in leaching, hydrometallurgy, are actually at low temperature. So there’s no reason you should plug it into the wall. You can use a lot of these fantastic renewable energy processes and technologies that are just running on to the market at the moment to lower the overall footprint. You should never look at this as a single problem. It is always a very coupled, complex problem of minerals processing, it’s about the altogether and that is the focus, the understanding that it’s not one discipline. We all have to work together. Just as much as we talk about data as this big trend, data is meaningless unless you apply and categorise it, and do something to it to turn it into something useful. The same thing applies to metallurgy. There are many opportunities for us to work together and bring interesting, transdisciplinary thinking into metallurgy to solve our big problems.
Some people are looking more closely at hydrometallurgy, and we know that the Kell process is already rolling out at the Sedibelo PGMs mine in the North West. Are there ways of doing things that are less energy intensive?
There are small niche applications. But again, I’m one of those big believers in looking at the life cycle, the larger scale ecosystem. If you’re looking at protecting elephants, for example, you’re not just trying to protect the elephants but the entire ecosystem that the elephants work and live in. So it’s very easy to say that we need to get rid of pyrometallurgy, but the ecosystem requires us to have pyrometallurgy, especially in bulk commodities, where you’ve got ferrochrome, ferromanganese, iron – we’re talking about massive bulk commodities. When you do something through a hydrometallurgy process, you really want it to already be concentrated. You want to do something to it, so you put the least effort into making it a metal. You never just put the run-of-mine ore into a smelter. You try to clean it up so that you don't waste energy. A lot of our effort has to go into putting the least possible waste into a process that just passes through the process and then has to be managed. That’s one of the challenges that we have with the hydrometallurgy processes is that they often have significant residues and waste that need to be stored, managed, cleaned up, whereas if you have a pyro process, and it’s not all through and equal, you often end up with a clean byproduct that you can just use as backfill.
What are you seeing that is really exciting you at the moment?
I’ve been very fortunate in my career to have had experience in an incredible number of commodities. For me at the moment, the two commodities that are really exciting me, because of the pressures that they were under, are ferrochrome and the PGMs industry. Both of these, in South Africa particularly, have been through stressful times and a lot of that is about the cost and availability of electricity. What’s really exciting me is how people have actually gone and absolutely thought outside the box to optimise their processes, to be competitive. In the last while, it’s been exciting to see, as the commodity prices have been booming, how people have just jumped in, and new people have entered the market.
What about more use being made of furnace off gas?
The ferrochrome industry already does that. What’s very interesting with ferrochrome is that when you look at the raw materials, about 30% of the product is metal, 30% is slag and 30% is gas. If you have a modern furnace, a closed furnace, that gas is really good quality CO2 and most of those in ferrochrome use that gas to preheat or dry or even generate electricity. Even the ilmenite smelters have been doing it probably for the last five years. So the furnace industry is definitely ahead of the curve but there’s definitely opportunities to use off gases to help you save your energy otherwise you just put it into the atmosphere without recovering any of that heat. Other exciting opportunities, of course, if your byproduct is slag, like say, for example, the PGMs industry, you have a massive slag byproduct that comes out molten at 1 500 oC or 1 600 oC, the next step would be to find a way to extract some of that waste heat from the slag.
Can't green hydrogen be used to a greater extent?
Obviously we want to use green hydrogen. That would be the best solution for everyone. But there are many processes that have a byproduct of the grey hydrogen. Now that you have hydrogen ready, you may as well use it. One of the things we have to say is, yes, it’s not the perfect solution but it’s worse to just let it go to waste. The second thing is that everyone who is working in South Africa towards the fuel cell economy – and there is quite a large investment by many companies. Anglo is already investing a lot in using fuel cells on the mine. So that’s an incredible opportunity for hydrogen to come into an actual useful application. I honestly believe that on all the big mines where we have a lot of big moving machinery you can move away from diesel and switch to a hydrogen-based fuel system because you have a contained ecosystem. I’m very excited about what I’m seeing and, of course, with us now being able to install this massive 100 MW independent producers’ energy, those doing so can start producing hydrogen from renewable energy. I think that we’re at this exciting evening before the big break, and I think we’re on the verge of people jumping into that. The mines are ready, and the furnaces are ready, and in Europe there’s a lot of work in iron making using hydrogen. Mintek is also doing work on that in collaboration with Europe. There’s a lot of interest in hydrogen and I think that definitely in South Africa something is going to come of it. The South African government, the Department of Science and Innovation, has been supporting this hydrogen economy concept for nearly 20 years. So there’s knowledge, there’s know-how, there are people who know what they are doing, so I think we’re on the verge of nice breakthroughs in hydrogen.
Is there anything more than can be done for junior miners and can they do more for themselves in the smelting area?
That’s a really good question, something that I’ve been grappling with for 25 years. For a long time, we’ve tried different models, for example, when Mintek offered even toll-smelting facilities. Juniors have access to ore but the bridging investment to get to smelter level is really high. It’s much easier to put up a couple of spirals, make concentrate and sell it because the barrier to entry is very challenging. So I don’t think there’s an easy answer, but what I’ve seen in the last year or so, as commodity prices are stronger now, is a lot more people are starting to get little smelters off the ground. That’s always a good sign because for the last almost 25 years, we’ve not been building new smelters. You have one or two exceptions but generally there have not been new entrants. Existing mining companies would build their furnaces bigger or modify them but there have not been a lot of new entrants. But in the last year or so, there have been new entrants. They’re not big yet but the fact that they’re learning how to smelt is important because it’s not just about money. It’s about getting the right people, it’s a complex process to run so people starting small is going to be the secret to getting new entrants into the market. The second thing is that our ores are starting to lean towards smaller facilities. You have PGM ore concentrates that are full of chrome and there are always little side tailings processes, so there’s going to be these different kinds of ores that are ideally suited to smaller furnace. I think it's a case of a lot of things have to go right. We have the technology, we have the ores and if we can get the renewable energy or the self-generation into place, people will be able to run their own smaller furnaces and build up knowledge and cash to then be able to build their bigger furnaces. So I honestly think the stars are aligning for the smaller guys.
And what about the waste collectors who push trolleys down the road, the urban miners? Is there anything that can enable these people to put their metals into a direct current (DC) furnace?
There’s actually a very interesting history around this. About ten years ago we started asking whether it is worth putting say electronic e-waste into a DC furnace. In that time at Mintek, we actually developed a process that did not use electricity but used gas. The idea was to build many small furnaces all over the country at collections points because e-waste is actually not that hard to process. Once you put it at high temperature, you can break down anything. The problem is collecting enough of it in a centralised point that is able to sort it because the solution for e-waste is actually about sorting and making sure that you sort it optimally, then there are a lot of technologies available. I think Mintek’s smelting process with gas has a huge potential for a smaller operator, a collector, to build up their own little smelter, produce the metal and then get into the market of separating the metals out. I think there’s a lot we can do. We need to get the right people together to talk to the collectors.
A specialist in DC arc furnace technologies, Geldenhuys has presented papers at several international conferences. Her research interests include DC furnace technology, ferrochromium, ferronickel, slag cleaning, and PGM smelting processes.
Her experience includes involvement in test work, process development, and scale-up of DC arc furnaces for ferrochromium, titania slag, ferronickel, the smelting of titaniferous magnetite, recycling of waste materials, and recovery of valuable commodities from discarded slags.
Comments
Press Office
Announcements
What's On
Subscribe to improve your user experience...
Option 1 (equivalent of R125 a month):
Receive a weekly copy of Creamer Media's Engineering News & Mining Weekly magazine
(print copy for those in South Africa and e-magazine for those outside of South Africa)
Receive daily email newsletters
Access to full search results
Access archive of magazine back copies
Access to Projects in Progress
Access to ONE Research Report of your choice in PDF format
Option 2 (equivalent of R375 a month):
All benefits from Option 1
PLUS
Access to Creamer Media's Research Channel Africa for ALL Research Reports, in PDF format, on various industrial and mining sectors
including Electricity; Water; Energy Transition; Hydrogen; Roads, Rail and Ports; Coal; Gold; Platinum; Battery Metals; etc.
Already a subscriber?
Forgotten your password?
Receive weekly copy of Creamer Media's Engineering News & Mining Weekly magazine (print copy for those in South Africa and e-magazine for those outside of South Africa)
➕
Recieve daily email newsletters
➕
Access to full search results
➕
Access archive of magazine back copies
➕
Access to Projects in Progress
➕
Access to ONE Research Report of your choice in PDF format
RESEARCH CHANNEL AFRICA
R4500 (equivalent of R375 a month)
SUBSCRIBEAll benefits from Option 1
➕
Access to Creamer Media's Research Channel Africa for ALL Research Reports on various industrial and mining sectors, in PDF format, including on:
Electricity
➕
Water
➕
Energy Transition
➕
Hydrogen
➕
Roads, Rail and Ports
➕
Coal
➕
Gold
➕
Platinum
➕
Battery Metals
➕
etc.
Receive all benefits from Option 1 or Option 2 delivered to numerous people at your company
➕
Multiple User names and Passwords for simultaneous log-ins
➕
Intranet integration access to all in your organisation