Supplier expanding new pump’s footprint in Australian market
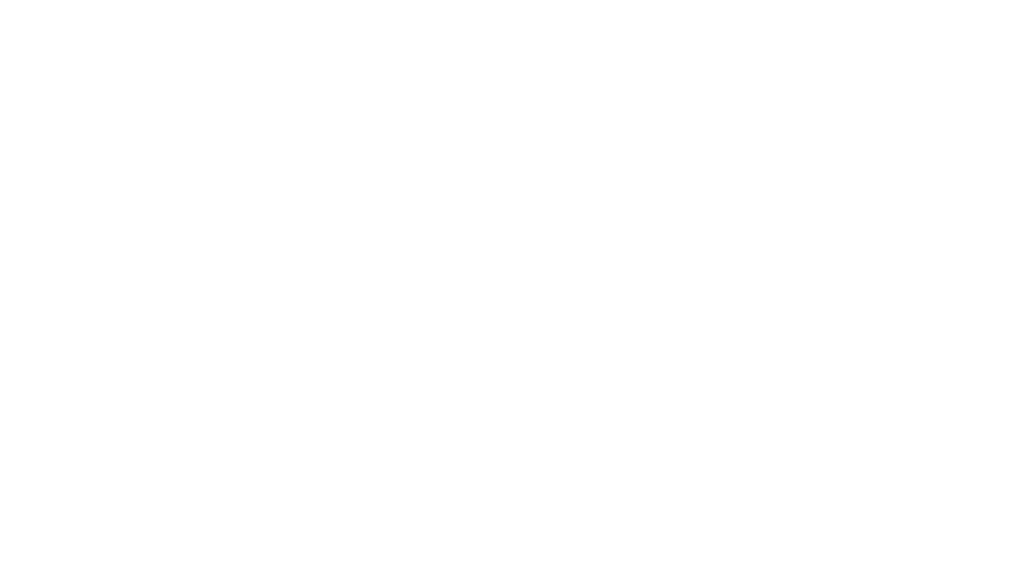
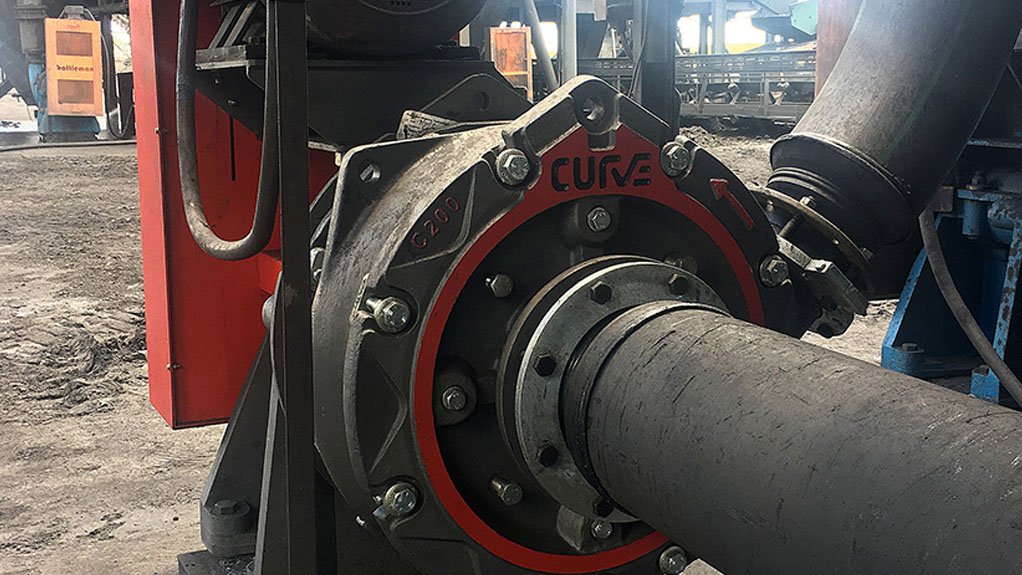
RUBBER LINER The Curve lines of pumps are rubber lined to help increase the resistance against abrasive and corrosive liquids
Heavy-duty pumps solutions company Pump & Abrasion Technologies (PAT) Australia introduced its new Curve range of slurry pumps at the Aimex mining show, in Sydney, to the New South Wales mining community, following the company’s success with the product in South Africa.
This year, the Aimex exhibition, held at the end of last month, had a strong focus on innovation, making it the perfect setting to introduce the Curve range, says PAT Australia.
PAT Australia business manager Gerhard van Vuuren explains that “the fresh approach to slurry pumping had an immediate and positive impact” on the South African and African mining industries.
“PAT took the exciting and bold step to design and manufacture a new range of slurry pumps, tailored specifically for the needs of the market. From a clean sheet, we applied the latest technology and came up with a range of slurry pumps called the Curve range,” he says.
Van Vuuren points out that the range provides customers with major improvements in total ownership cost (TOC), improved efficiency, lower power consumption throughout the pump’s life cycle, improved overall safety, and reduced parts wear life and maintenance requirements.
With its global vision, he says, the next step for the company after the successes of the Curve pumps in South Africa, where its head office is based in Centurion, is to enter the Australian market and expand the Curve footprint. “After an in-depth analysis of the Australian market, Western Australia was chosen as the starting point for the Australian operations.”
In April, PAT Australia was registered and a highly specialised team was assembled to develop and grow its Australian business. Van Vuuren highlights that one of the important additions that the company has made is the appointment of PAT Australia sales manager Ian Moulsdale.
“In 22 years, I have not seen this big a step-up in pumping technology and design. It was an easy decision to become part of this great product – without a doubt, the best company, best people and best product I have worked with in a very long time,” Moulsdale enthuses.
Van Vuuren points out that, during the first four months of operation in Australia, PAT Australia has managed to install Curve pumps at two Western Australian customers’ processing sites.
“The results have been tremendous, with customers reducing their TOC by up to 59%, with a 100% reduction on gland seal water requirements, owing to a superior dry gland seal arrangement, ease of maintenance, the pump’s longer service life, compared with conventional slurry pumps, and improved safety while undertaking maintenance.
PAT Australia is focused on a future where it continues to support its customers’ needs through the Curve range of slurry pumps, making its customers’ operations more cost efficient, while improving the safety of employees.
In March, Mining Weekly reported that, following the launch of the Curve range of pumps in September 2016, a North West-based ferrochrome producer has installed the new Curve series pumps at its plant.
The ferrochrome producer now plans to replace all its pumps at one of its plants with the Curve range. The conversion project started with the installation of the first pump in November 2016.
PAT sales director James Pienaar says the installation was, in effect, the “first true test” of the Curve S150 pump. “The changeover of all existing pumps at the customer’s processing plant to the Curve range is a process that takes time, but we are . . . close to [having] ten Curve pumps . . . installed and operating at that specific plant.”
The Curve S150 model offers several innovative features that make it the ideal choice for the ferrochrome customer’s operational needs. These features include fully profiled impeller vanes, an adjustable throatbush, an enhanced cutwater profile and a clip-in suction joint.
Sealing performance and pump life have been enhanced by a larger-diameter expeller and high chrome shaft sleeve and lantern ring. The Curve S150 also features a discharge piece designed to eliminate the need to remove the discharge pipe during routine maintenance.
To date, the Curve pumps at this processing plant operation have produced a 73% reduction in downtime, as they are opened only every third maintenance cycle, owing to its longer wear life. Maintenance time and cost reduction were measured in terms of the wear life and required maintenance of the previously installed pumps.
Further, the Curve pumps’ encapsulated one-piece volute liner reduces opening and closing time by 80%, eye bolts allow for safe removal of the casing, the casing assembly is a balanced load for safe handling, and the discharge pipe no longer needs to be removed when opening the pump because of the newly designed discharge piece.
Pienaar adds that the Curve pumps also reduced electricity consumption. “An 8% power reduction was reported . . . [because of] the improved impeller and volute profile design. Slurry flows through the pump in a more natural flow pattern.”
A 52% reduction in TCO was also reported. These results prove the Curve range’s ability to outperform older-technology pumps on the market, he says, adding that the basic specifications of the previous pump and the Curve pump in the trial application were virtually the same.
Both pumps have rubber liners and a 35% chrome impeller. In terms of expected performance, both pumps offer 38 ℓ/s. The duty covered by both pumps is the transfer to plant, with a particle size of 80% less than 1.5 mm. However, the Curve S150 operates 50% slower in this application, thereby significantly reducing wear and power consumption.
Comments
Press Office
Announcements
What's On
Subscribe to improve your user experience...
Option 1 (equivalent of R125 a month):
Receive a weekly copy of Creamer Media's Engineering News & Mining Weekly magazine
(print copy for those in South Africa and e-magazine for those outside of South Africa)
Receive daily email newsletters
Access to full search results
Access archive of magazine back copies
Access to Projects in Progress
Access to ONE Research Report of your choice in PDF format
Option 2 (equivalent of R375 a month):
All benefits from Option 1
PLUS
Access to Creamer Media's Research Channel Africa for ALL Research Reports, in PDF format, on various industrial and mining sectors
including Electricity; Water; Energy Transition; Hydrogen; Roads, Rail and Ports; Coal; Gold; Platinum; Battery Metals; etc.
Already a subscriber?
Forgotten your password?
Receive weekly copy of Creamer Media's Engineering News & Mining Weekly magazine (print copy for those in South Africa and e-magazine for those outside of South Africa)
➕
Recieve daily email newsletters
➕
Access to full search results
➕
Access archive of magazine back copies
➕
Access to Projects in Progress
➕
Access to ONE Research Report of your choice in PDF format
RESEARCH CHANNEL AFRICA
R4500 (equivalent of R375 a month)
SUBSCRIBEAll benefits from Option 1
➕
Access to Creamer Media's Research Channel Africa for ALL Research Reports on various industrial and mining sectors, in PDF format, including on:
Electricity
➕
Water
➕
Energy Transition
➕
Hydrogen
➕
Roads, Rail and Ports
➕
Coal
➕
Gold
➕
Platinum
➕
Battery Metals
➕
etc.
Receive all benefits from Option 1 or Option 2 delivered to numerous people at your company
➕
Multiple User names and Passwords for simultaneous log-ins
➕
Intranet integration access to all in your organisation