Supplier replaces pump seals at coal mine
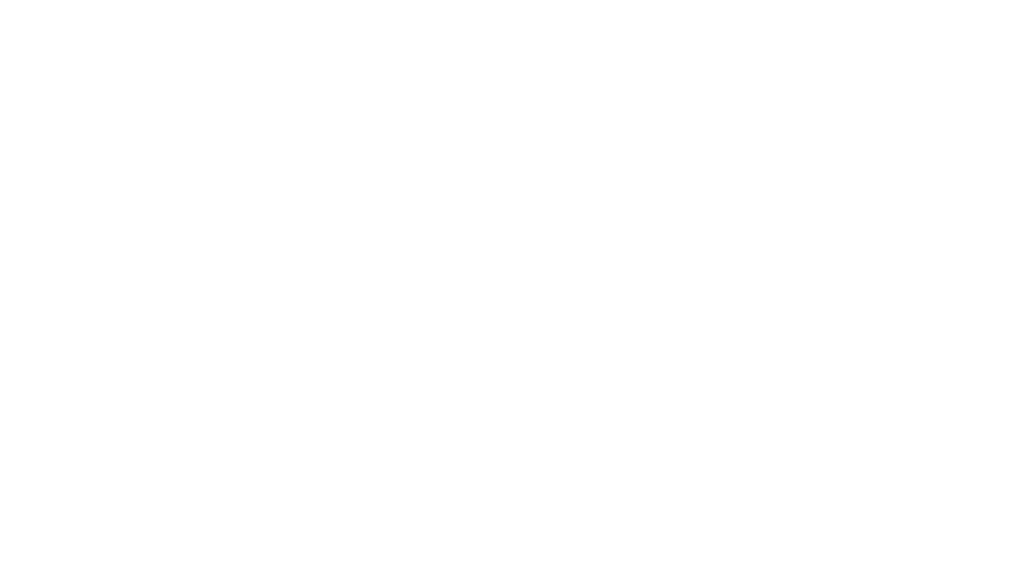
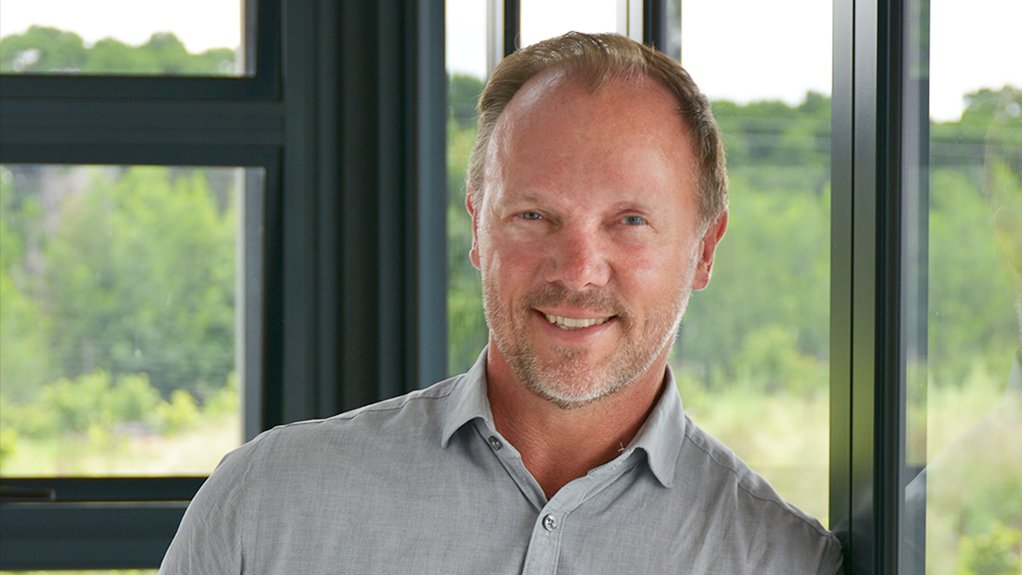
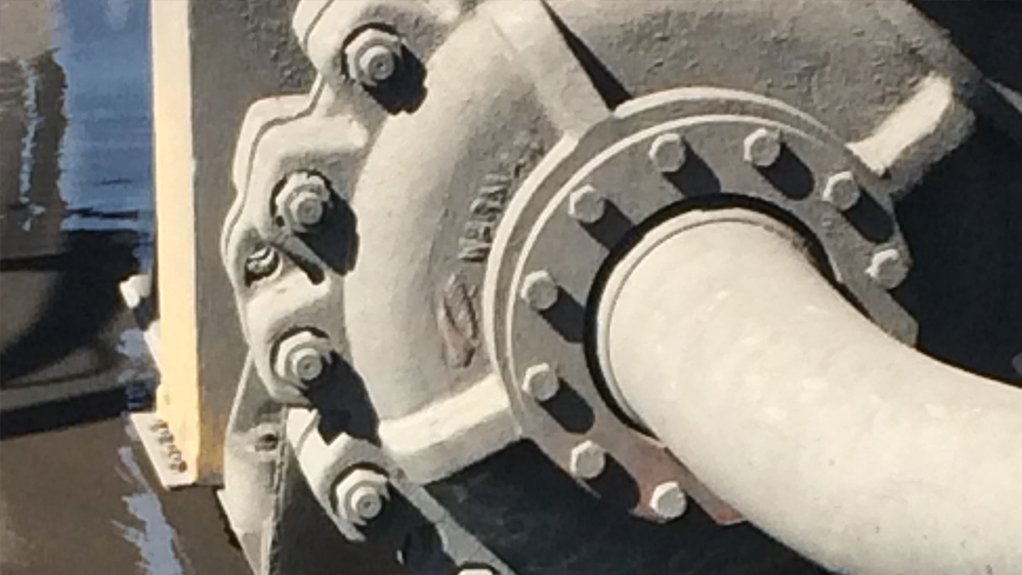
FRANSCOIS STEENKAMP Fitting an incorrect sealing solution can cause damage to bearings, owing to excessive leakage from the pump
A ‘SLURRY’OUS ISSUE A centrifugal pump showing slurry leakage
Mechanical seals, pumps and complementary pumps products supplier Mechanical Rotating Solutions (MRS) replaced expeller seals on centrifugal pumps at a coal mining company’s facility in Mpumalanga at the end of April and beginning of May; the pumps were registering poor mean time between failures.
The pumps were originally sealed using conventional mechanical packing that, along with poor adherence to the packing schedule, caused excessive slurry leakage and, consequently, damage to the pump bearings, owing to water ingress, MRS CEO Franscois Steenkamp explains.
As a result, MRS replaced the conventional seals with AESSEAL SMSS single monolithic stationary seals, which improved the efficiency of the high-pressure pumpset of coal processing plant and also eliminated some of the main causes of premature seal failure.
“Since installing the AESSEAL SMSS seal solution, the reliability of the pumps has improved significantly. There is no damage to the shaft from fretting or to the bearings from water leakage. There has also been a significant reduction in water consumption at the mine,” says Steenkamp.
The SMSS is part of the AESSEAL modular sealing system range distributed by MRS, the official distributor of all AESSEAL products in Mpumalanga.
“In addressing the client’s needs, the stationary seal face is spring-loaded, which compensates for angular misalignment between the shaft and the housing,” he explains.
As part of the Mpumalanga project, the company further installed a CDPH double mechanical seal complemented by an AESSEAL SW2 water management system and South African Seal Water Units, with the units each containing a 200 ℓ capacity.
The water line acts as the system’s fluid and pressure source to feed the mechanical seal with a clean, cool and stable water-barrier fluid.
The plant’s water line pressure can be adjusted so that the barrier fluid pressure within the system is maintained at 1 bar above stuffing box pressure, resulting in a pressure differential that keeps harmful products away from mechanical seal faces and increases seal and pump reliability.
The system also uses an integral vessel to store flushing water for continuous recycling.
The AESSEAL range offers various seal and liner configurations that enable MRS to tailor a solution to client-specific applications.
The company has installed various AESSEAL solutions at mining operations throughout Mpumalanga, resulting in significant savings for clients.
“We advise our clients on the pros and cons of mechanical seals over traditional seals, and assist them in making the right decision to suit their needs. Our range of seals provide maximum face stability in high-pressure and -temperature applications, improving seal life while reducing damage to faces in stop/start applications,” Steenkamp adds.
Pumps Challenges
Gland packing is often used to seal centrifugal slurry pumps at mines, owing to its being more cost effective.
Steenkamp notes, however, that this method uses large quantities of water, causes pump shaft damage and requires frequent maintenance and replacement.
Hence, he cautions that fitting an incorrect sealing solution from the outset can cause damaged bearings, owing to excessive leakage from the pump, which, in turn, increases maintenance costs and downtime.
“The truth is that this traditional way of sealing pumps will cost more in the long term as a direct result of premature pump failure, increased leakage, higher energy usage and shaft sleeve damage, whereas mechanical seals can save up to 20% in kilowatts consumed.”
Further, when sealing a centrifugal pump, the challenge lies in allowing for a rotating shaft to enter the ‘wet’ area of the pump without allowing for large volumes of pressurised fluid to escape.
However, equipment reliability can be improved by changing the seal environment or upgrading the seal design, with MRS, for example, providing inexpensive seal conversion kits to upgrade non-AESSEAL designs or change the original-equipment manufacturer’s seal environment to improve seal life, Steenkamp explains.
Further, while a properly installed, quality mechanical seal will contribute to productivity and the life span of the pumps, correctly using seal support systems can also extend equipment seal life.
Meanwhile, MRS launched its mobile pump venture in December last year, but has also noticed demand for its complementary pump products.
As an African agent for STRAUB pipe couplings, MRS is assisting mining operations in switching from traditional pipe joints to the STRAUB system that can replace welded, flanged, threaded or grooved pipe joints in minutes.
Steenkamp says this increases productivity because individual bolts do not have to be removed by hand and it eliminates the need for using a cutting torch, which may take up to two hours when pump maintenance is required.
Moreover, the company is assisting mining operations aiming to implement water-saving measures by incorporating pumps systems and products designed to address water wastage.
“The variety of industry-proven mechanical seals offered by MRS is only part of a total rotating equipment sealing solution. As more industry partners see the advantage of mechanical seals that improve reliability, increase pump-seal life and save time and money, the importance of protecting the rest of the pump becomes clear,” he concludes.
Comments
Press Office
Announcements
What's On
Subscribe to improve your user experience...
Option 1 (equivalent of R125 a month):
Receive a weekly copy of Creamer Media's Engineering News & Mining Weekly magazine
(print copy for those in South Africa and e-magazine for those outside of South Africa)
Receive daily email newsletters
Access to full search results
Access archive of magazine back copies
Access to Projects in Progress
Access to ONE Research Report of your choice in PDF format
Option 2 (equivalent of R375 a month):
All benefits from Option 1
PLUS
Access to Creamer Media's Research Channel Africa for ALL Research Reports, in PDF format, on various industrial and mining sectors
including Electricity; Water; Energy Transition; Hydrogen; Roads, Rail and Ports; Coal; Gold; Platinum; Battery Metals; etc.
Already a subscriber?
Forgotten your password?
Receive weekly copy of Creamer Media's Engineering News & Mining Weekly magazine (print copy for those in South Africa and e-magazine for those outside of South Africa)
➕
Recieve daily email newsletters
➕
Access to full search results
➕
Access archive of magazine back copies
➕
Access to Projects in Progress
➕
Access to ONE Research Report of your choice in PDF format
RESEARCH CHANNEL AFRICA
R4500 (equivalent of R375 a month)
SUBSCRIBEAll benefits from Option 1
➕
Access to Creamer Media's Research Channel Africa for ALL Research Reports on various industrial and mining sectors, in PDF format, including on:
Electricity
➕
Water
➕
Energy Transition
➕
Hydrogen
➕
Roads, Rail and Ports
➕
Coal
➕
Gold
➕
Platinum
➕
Battery Metals
➕
etc.
Receive all benefits from Option 1 or Option 2 delivered to numerous people at your company
➕
Multiple User names and Passwords for simultaneous log-ins
➕
Intranet integration access to all in your organisation