Testing at Multotec improves manganese recoveries
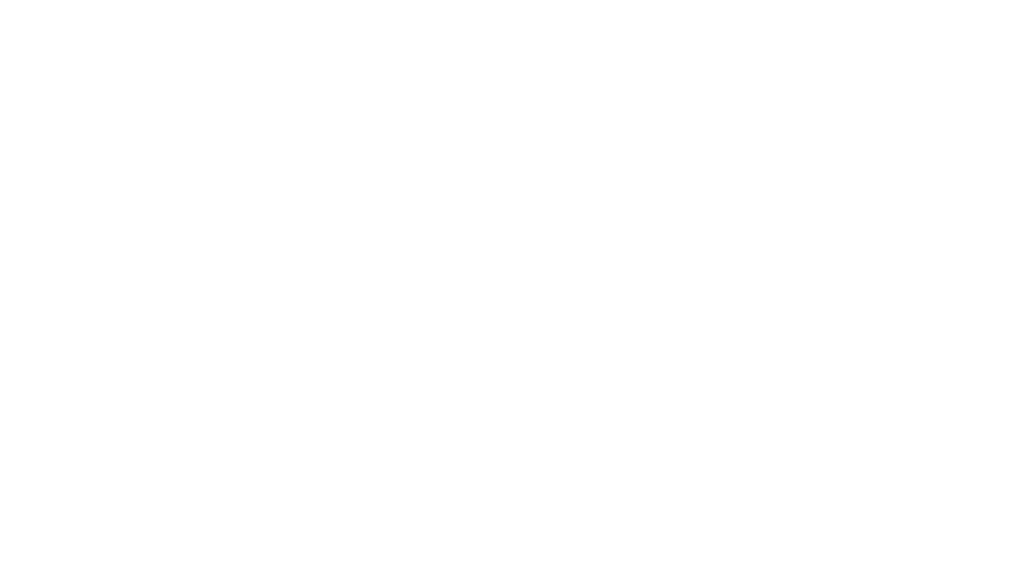
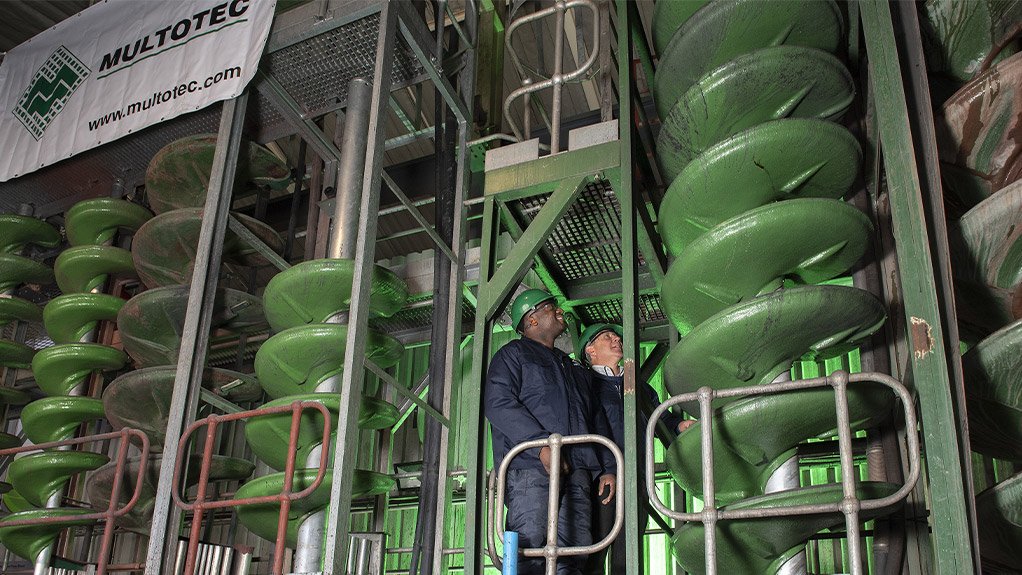
Better recoveries were achieved during test work using the spiral concentrators together with the wet high-intensity magnetic separator (WHIMS) at Multotec’s in-house test facility
Using its extensive in-house testing facility for material from a South African manganese producer, Multotec has defined a solution that will upgrade the quality of saleable concentrate while reducing the content of manganese in tailings.
According to Faan Borman, technology manager : research and development at Multotec’s technology division, the customer had specific targets they wanted to reach. These targets aim to optimise revenue from recovered minerals and also improve environmental performance, as a level of more than 10% manganese in the tailings would require the dump to be classified as hazardous.
“The test work we conducted was to improve recovery of ultra-fine material from the thickener underflow,” says Borman. “The financial benefit of better recoveries is to produce a richer concentrate, but it is also to reduce the metal content in tailings – so that it would not be regarded as hazardous waste.”
Two sets of test work were designed and conducted. In the first set, stockpile material with a metal grade of 16% was tested using Multotec’s UX7 ultra-fine spiral concentrator for the roughing and scavenging phases, while its SC21 five-turn spiral was used for the cleaning stage. This allowed the target saleable grade of 32% to be achieved, he says, but there was still some work to be done to reach the tailings target grade.
“This required some out-of-the-box thinking for the second set of tests, where we ran the material over the wet high-intensity magnetic separator (WHIMS) with a vertical ring,” he says. “At the highest intensity, this was able to downgrade the spiral tailings material from 13 to 14% right down to 7% manganese – a significant improvement.”
He highlighted that for process plants to achieve the most viable solutions they must optimise the use of cost effective equipment and strategies. Given the higher cost of applying WHIMS technology, the testing procedure using spirals was able to remove gangue minerals and reduce the volume of bulk material before being treated by the WHIMS.
“Another benefit of this process was that about a third of the material sent to the WHIMS in this process could be returned to the spiral circuit for further upgrade to meet specifications,” he notes. “This considerably reduces tailings volumes, potentially cutting down the footprint of the tailings storage facility and extending its lifespan.”
Bornman says that the cost of managing tailings facilities in a compliant manner, and the tightening regulations and policies on tailings dams, are encouraging a trend to re-process them. Technology improvements in metal recovery over the years now makes these re-treatment efforts commercially attractive.
“We have had considerable success in applying the spirals together with the WHIMS, as it is key to ensure sufficient bulk reduction up front,” he says. “The process can be applied across a range of commodities, and we have also seen good results in minerals including chrome, iron ore, lithium and mineral sands.”
Comments
Press Office
Announcements
What's On
Subscribe to improve your user experience...
Option 1 (equivalent of R125 a month):
Receive a weekly copy of Creamer Media's Engineering News & Mining Weekly magazine
(print copy for those in South Africa and e-magazine for those outside of South Africa)
Receive daily email newsletters
Access to full search results
Access archive of magazine back copies
Access to Projects in Progress
Access to ONE Research Report of your choice in PDF format
Option 2 (equivalent of R375 a month):
All benefits from Option 1
PLUS
Access to Creamer Media's Research Channel Africa for ALL Research Reports, in PDF format, on various industrial and mining sectors
including Electricity; Water; Energy Transition; Hydrogen; Roads, Rail and Ports; Coal; Gold; Platinum; Battery Metals; etc.
Already a subscriber?
Forgotten your password?
Receive weekly copy of Creamer Media's Engineering News & Mining Weekly magazine (print copy for those in South Africa and e-magazine for those outside of South Africa)
➕
Recieve daily email newsletters
➕
Access to full search results
➕
Access archive of magazine back copies
➕
Access to Projects in Progress
➕
Access to ONE Research Report of your choice in PDF format
RESEARCH CHANNEL AFRICA
R4500 (equivalent of R375 a month)
SUBSCRIBEAll benefits from Option 1
➕
Access to Creamer Media's Research Channel Africa for ALL Research Reports on various industrial and mining sectors, in PDF format, including on:
Electricity
➕
Water
➕
Energy Transition
➕
Hydrogen
➕
Roads, Rail and Ports
➕
Coal
➕
Gold
➕
Platinum
➕
Battery Metals
➕
etc.
Receive all benefits from Option 1 or Option 2 delivered to numerous people at your company
➕
Multiple User names and Passwords for simultaneous log-ins
➕
Intranet integration access to all in your organisation