Weba custom Chute solution tackles sticky ore challenge in Caribbean gold mine
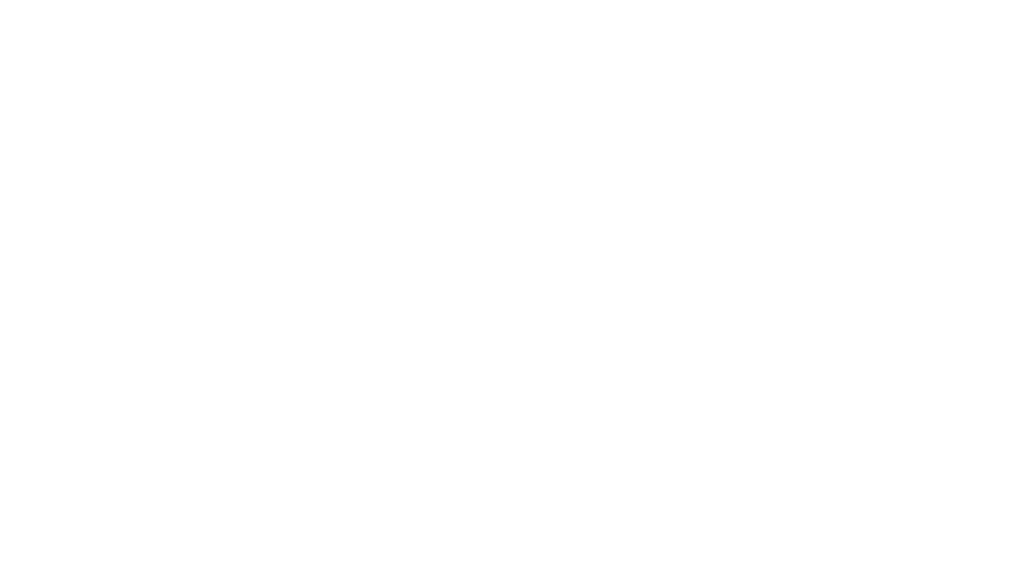
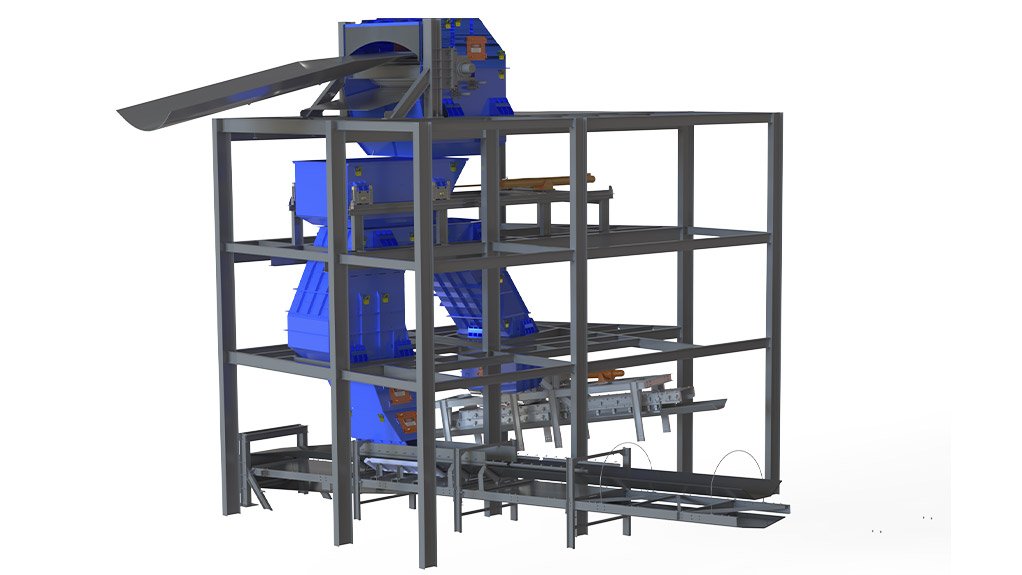
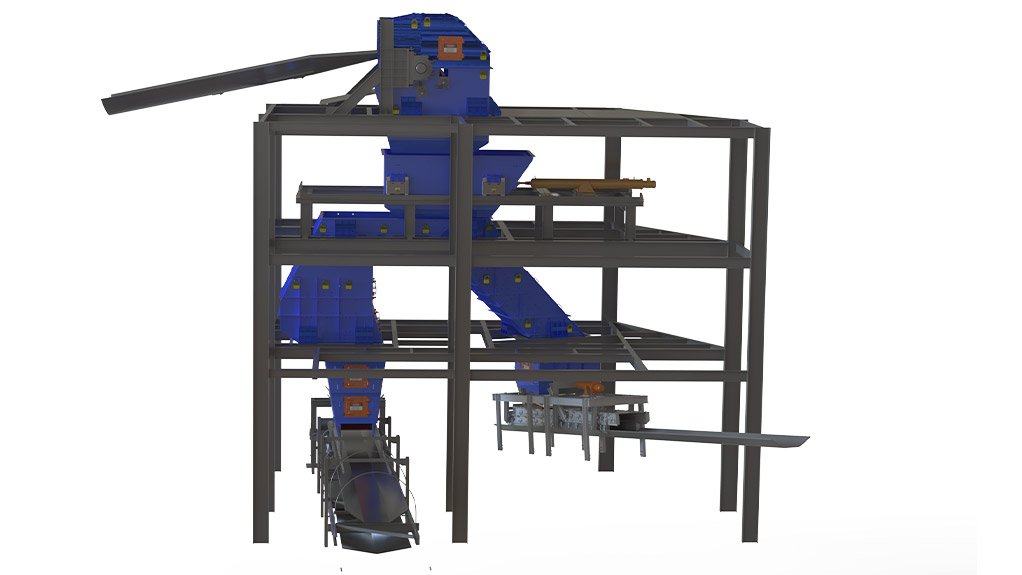

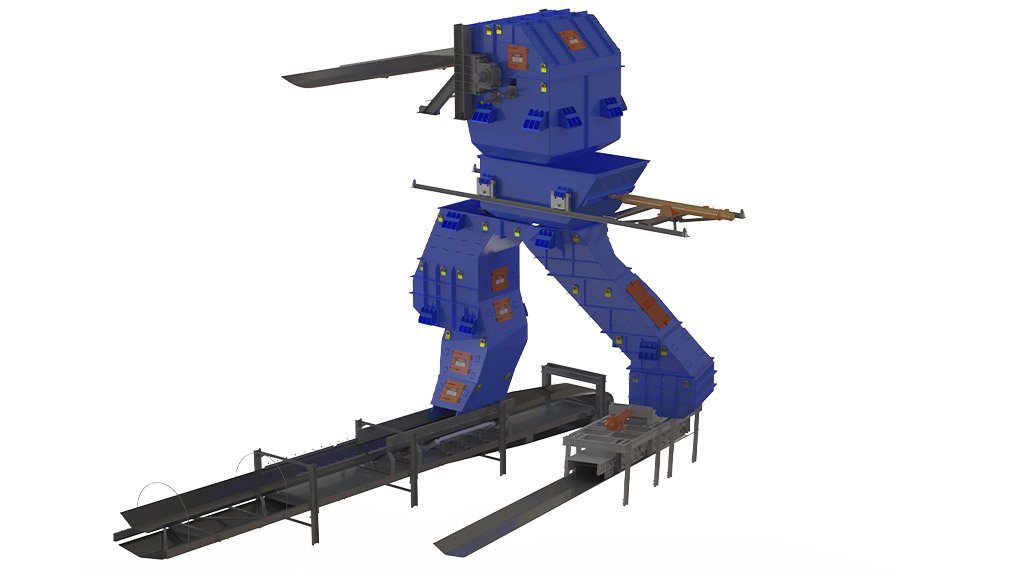

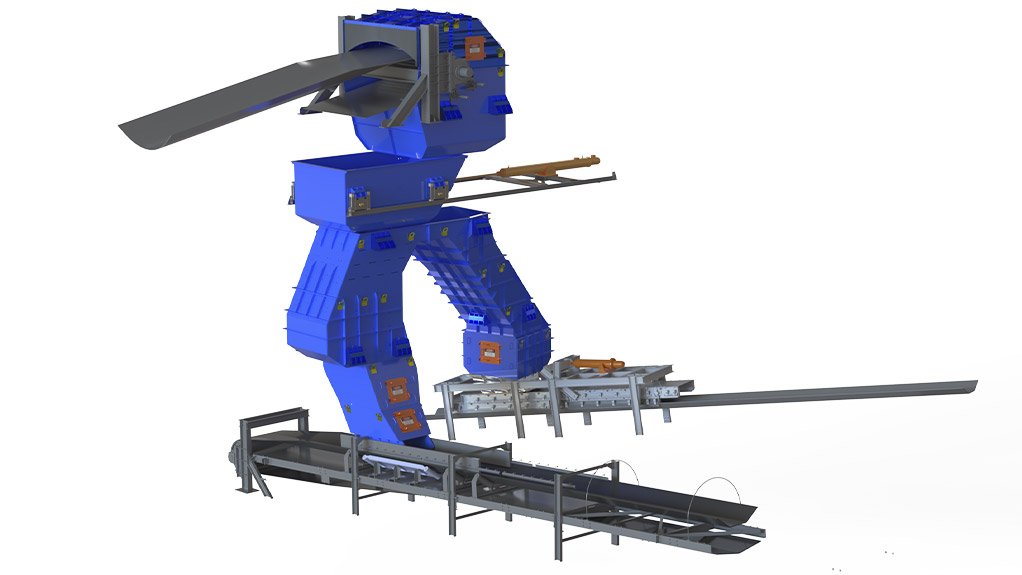
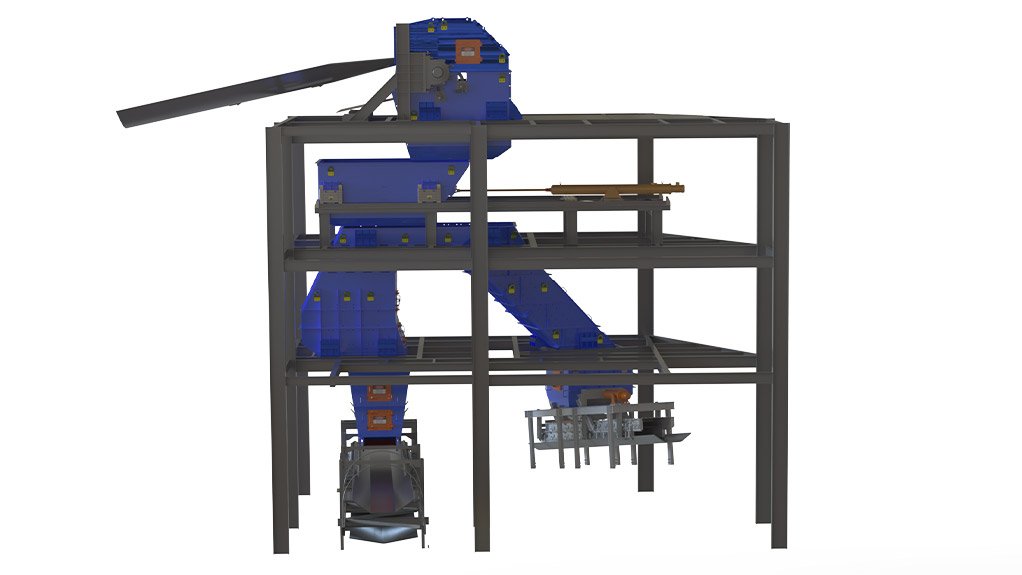
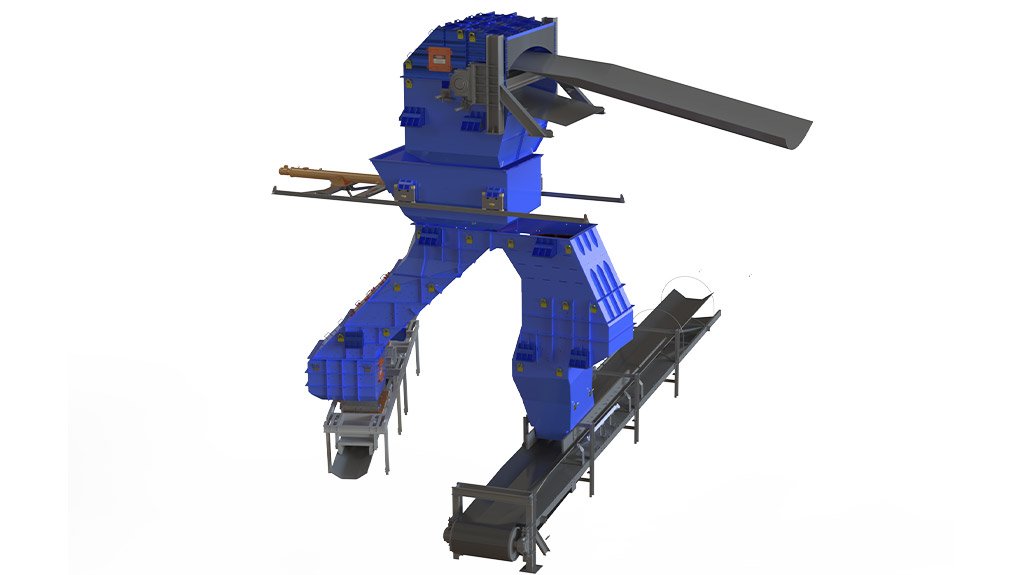
The newly installed Weba Chute System at a gold mining operation in the Caribbean was custom-engineered to handle sticky ore at a challenging transfer point
The custom-engineered Weba Chute System installed at the fixed crushing station effectively resolves material flow challenges caused by sticky ore
Designed for a fixed crushing station, the three-storey chute structure ensures controlled transfer of run-of-mine ore from the conveyor system
Within the fixed crushing station, the main chute features Weba’s dead box design, enabling a protective ore layer to reduce wear and maintenance
To suit the layout of the fixed crushing station, the chute was engineered with bifurcated flow paths to handle different ore flow volumes
The chute’s design in the fixed crushing station included a relocated head pulley position, optimised through discrete element modelling (DEM) analysis
Integrated into the fixed crushing station, the chute incorporates reverse-flow sections to reduce ore velocity and limit impact-related wear
Installed as part of the fixed crushing station, the Weba chute solution ensures reliable, uninterrupted material flow under demanding site and ore conditions
This article has been supplied.
An expanding gold mining operation in the Caribbean recently faced a significant challenge at one of its transfer points, where sticky ore - especially problematic during the hot summer months - was causing blockages and excessive maintenance.
To solve the issue, the mine turned to South Africa-based Weba Chute Systems, renowned for its custom-engineered transfer point solutions. According to Technical Manager Dewald Tintinger, the problematic chute was a large 10 metre or three-storey-high transfer point that received run-of-mine ore from a conveyor. However, the original placement of the head pulley was not conducive to smooth material flow.
“One of the core benefits of Weba Chute Systems is our dead box design, which allows material to form a protective layer on the chute’s internal surfaces,” says Tintinger. “This not only significantly reduces wear but also extends the chute’s service life and lowers total cost of ownership.”
He adds that the dead box design also minimises maintenance, avoiding the frequent liner replacements required with conventional steel-lined chutes, saving time, cost and improving safety.
To effectively channel the sticky ore, Weba Chute Systems engineered a large bifurcated chute. The main chute was designed at a precise angle to allow the bulk of the ore to flow freely through the dead box section, while a smaller chute with liners accommodated a minor portion of the material.
Crucially, implementing this design required relocating the head pulley. “We conducted extensive investigations including sampling and testing the ore to understand its flow characteristics,” Tintinger explains. “By calibrating our discrete element modelling (DEM) software with real test data - including static and dynamic angle of repose - we were able to define the exact positioning of the head pulley for optimal flow.”
Given the height of the transfer point, another key consideration was managing material velocity. “To control the speed and impact of the ore, we included reverse-flow sections within the chute,” he notes. “These strategically interrupt the trajectory, reducing wear and the need for ongoing maintenance.”
Tintinger concludes that the project highlights Weba Chute Systems’ ability to solve even the most demanding materials handling issues through customised engineering. “This installation is another example of how our solutions deliver lasting value, even in complex and remote mining environments.”
Comments
Press Office
Announcements
What's On
Subscribe to improve your user experience...
Option 1 (equivalent of R125 a month):
Receive a weekly copy of Creamer Media's Engineering News & Mining Weekly magazine
(print copy for those in South Africa and e-magazine for those outside of South Africa)
Receive daily email newsletters
Access to full search results
Access archive of magazine back copies
Access to Projects in Progress
Access to ONE Research Report of your choice in PDF format
Option 2 (equivalent of R375 a month):
All benefits from Option 1
PLUS
Access to Creamer Media's Research Channel Africa for ALL Research Reports, in PDF format, on various industrial and mining sectors
including Electricity; Water; Energy Transition; Hydrogen; Roads, Rail and Ports; Coal; Gold; Platinum; Battery Metals; etc.
Already a subscriber?
Forgotten your password?
Receive weekly copy of Creamer Media's Engineering News & Mining Weekly magazine (print copy for those in South Africa and e-magazine for those outside of South Africa)
➕
Recieve daily email newsletters
➕
Access to full search results
➕
Access archive of magazine back copies
➕
Access to Projects in Progress
➕
Access to ONE Research Report of your choice in PDF format
RESEARCH CHANNEL AFRICA
R4500 (equivalent of R375 a month)
SUBSCRIBEAll benefits from Option 1
➕
Access to Creamer Media's Research Channel Africa for ALL Research Reports on various industrial and mining sectors, in PDF format, including on:
Electricity
➕
Water
➕
Energy Transition
➕
Hydrogen
➕
Roads, Rail and Ports
➕
Coal
➕
Gold
➕
Platinum
➕
Battery Metals
➕
etc.
Receive all benefits from Option 1 or Option 2 delivered to numerous people at your company
➕
Multiple User names and Passwords for simultaneous log-ins
➕
Intranet integration access to all in your organisation