Copper smelter refractory installation completed
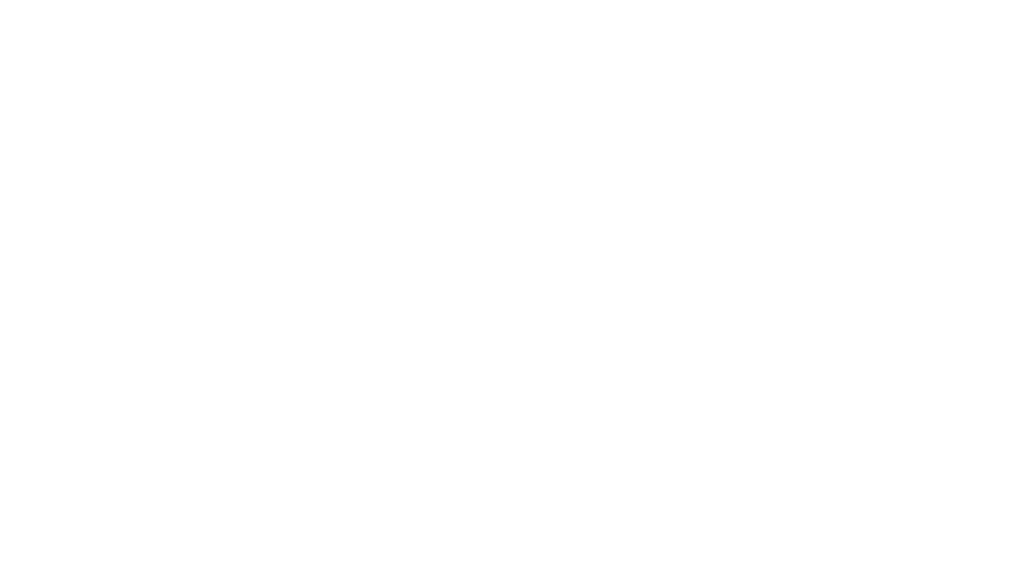
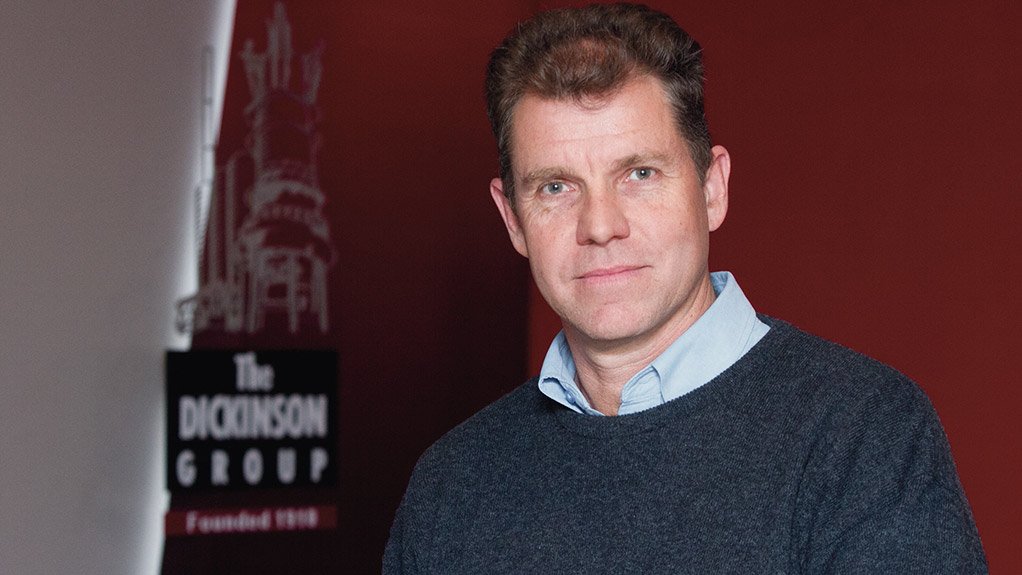
TREVOR DICKINSON The company’s involvement in Zambia has been part of Dickinson Group’s accelerated expansion outside South Africa
South African furnace and industrial services provider Dickinson Group successfully installed refractories at the copper smelter of the Kansanshi mine, in Solwezi, Zambia, in March, CEO Trevor Dickinson tells Mining Weekly.
Dickinson Group’s R30-million contract, which started in August 2014, entailed the installation of refractories to a matte settling electric furnace, an Isasmelt furnace, four Pierre-Smith converters, two Anode furnaces and two incinerators.
Dickinson Group employed about 110 people to complete the project.
The smelter, which produced its first copper in December 2014, and the adjacent mine are owned and operated by Zambian mining parastatal Zambia Consolidated Copper Mines Investment Holding (ZCCM-IH) and Canadian mining and metals company First Quantum Minerals (FQM) subsidiary Kansanshi Mining.
FQM invested over $800-million to develop the copper smelter, which is expected to produce more than 300 000 t/y of copper.
Outward Response
Dickinson explains the group’s involvement in Zambia has been part of the company’s accelerated expansion outside South Africa in response to the sluggish local economy, with very few new smelters being built.
Dickinson Group previously partnered with FQM and ZCCM-IH in Zambia when it completed the R13-million smelter shutdown and rebuild project at the Mopani copper mine, in June last year. The company continues to provide refractory maintenance services for the smelter, which is owned by joint venture company Carlisa Investments Corporation, comprising FQM, ZCCM-IH and mining major Glencore.
In addition, Dickinson Group provides sitewide smelter services for the Mozal smelter, near Maputo, in Mozambique, Dickinson says. Although the smelter is currently owned by diversified global major BHP Billiton, an imminent demerger will result in the company being operated by independent global metals and mining company South32.
Further, Dickinson notes that Dickinson Group is set to refurbish mining and smelting company BCL’s copper smelter in Selebi Phikwe, Botswana, in July. The refurbishment will include the rebuilding of the smelter’s copper flash furnace and its slag-cleaning furnace.
The refurbishment, which is required every five to eight years, will require a major shutdown of the smelter. Dickinson explains that the process will involve removing the remaining copper inside the flash furnace and replacing the existing refractory lining.
Dickinson Group COO Ralph van der Merwe tells Mining Weekly that the winter months are typically busy for the company, as many companies choose to do repairs and replacement during this time when electricity prices are higher.
Dickinson stresses that all the company’s operations outside South Africa are positive, as they contribute to diversifying the business.
The group has also diversified its operations in South Africa through offering a new range of industrial services, such as bulk silo cleaning and industrial vacuumation services, to the cement, copper and aluminium industries.
Van der Merwe explains that this diversification was necessary, as many smelting companies are delaying maintenance to their smelters primarily because they have not operated at full capacity, owing to slow commodity demand.
Dickinson notes that owing to Dickinson Group’s experience in large industrial processes, the company is well suited to the diversification it has pursued, adding that he has witnessed similar business-model expansions internationally.
New Technology
Dickinson Group received a large order from steel manufacturing corporation ArcelorMittal in April to manufacture new precast refractory modules which are used for the repair of coke ovens.
The modules are a faster installation method and also reduce gas emissions, and will be used at ArcelorMittal’s steel plant in Vanderbijlpark, Gauteng.
The Modular Cast Block, developed and patented by US manufacturers Vanocur Refractories, has been successfully used by ArcelorMittal at its Dofasco steel plant, in Canada, to reduce emissions, which tend to be problematic when using coke ovens, concludes Dickinson.
Comments
Announcements
What's On
Subscribe to improve your user experience...
Option 1 (equivalent of R125 a month):
Receive a weekly copy of Creamer Media's Engineering News & Mining Weekly magazine
(print copy for those in South Africa and e-magazine for those outside of South Africa)
Receive daily email newsletters
Access to full search results
Access archive of magazine back copies
Access to Projects in Progress
Access to ONE Research Report of your choice in PDF format
Option 2 (equivalent of R375 a month):
All benefits from Option 1
PLUS
Access to Creamer Media's Research Channel Africa for ALL Research Reports, in PDF format, on various industrial and mining sectors
including Electricity; Water; Energy Transition; Hydrogen; Roads, Rail and Ports; Coal; Gold; Platinum; Battery Metals; etc.
Already a subscriber?
Forgotten your password?
Receive weekly copy of Creamer Media's Engineering News & Mining Weekly magazine (print copy for those in South Africa and e-magazine for those outside of South Africa)
➕
Recieve daily email newsletters
➕
Access to full search results
➕
Access archive of magazine back copies
➕
Access to Projects in Progress
➕
Access to ONE Research Report of your choice in PDF format
RESEARCH CHANNEL AFRICA
R4500 (equivalent of R375 a month)
SUBSCRIBEAll benefits from Option 1
➕
Access to Creamer Media's Research Channel Africa for ALL Research Reports on various industrial and mining sectors, in PDF format, including on:
Electricity
➕
Water
➕
Energy Transition
➕
Hydrogen
➕
Roads, Rail and Ports
➕
Coal
➕
Gold
➕
Platinum
➕
Battery Metals
➕
etc.
Receive all benefits from Option 1 or Option 2 delivered to numerous people at your company
➕
Multiple User names and Passwords for simultaneous log-ins
➕
Intranet integration access to all in your organisation