Zimbabwe underground automation project progresses
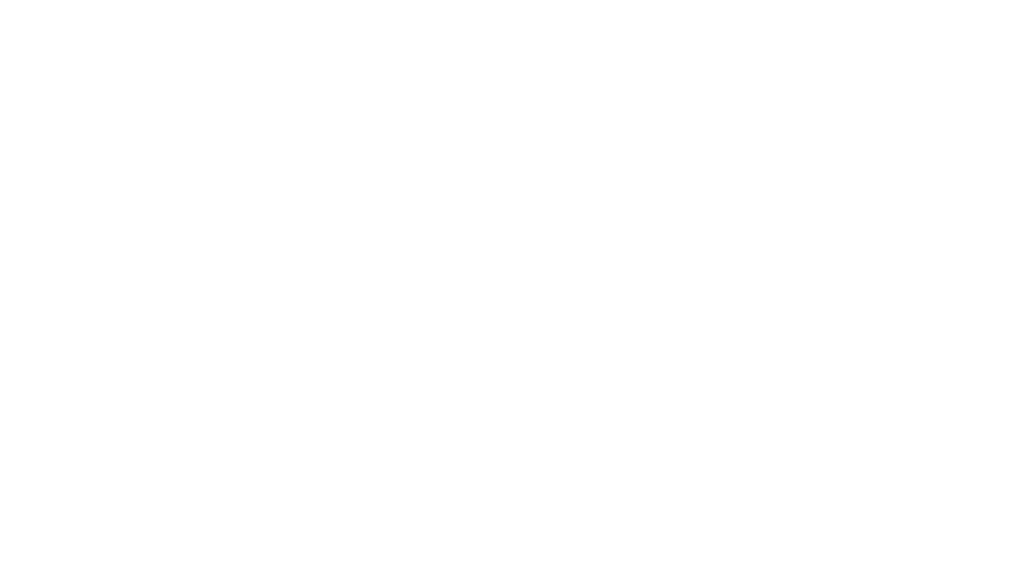
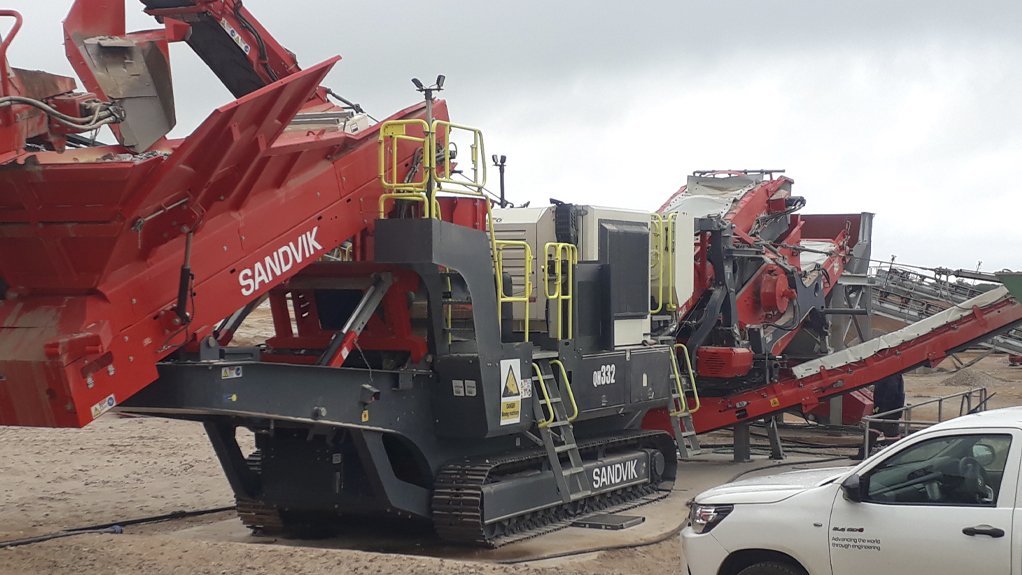
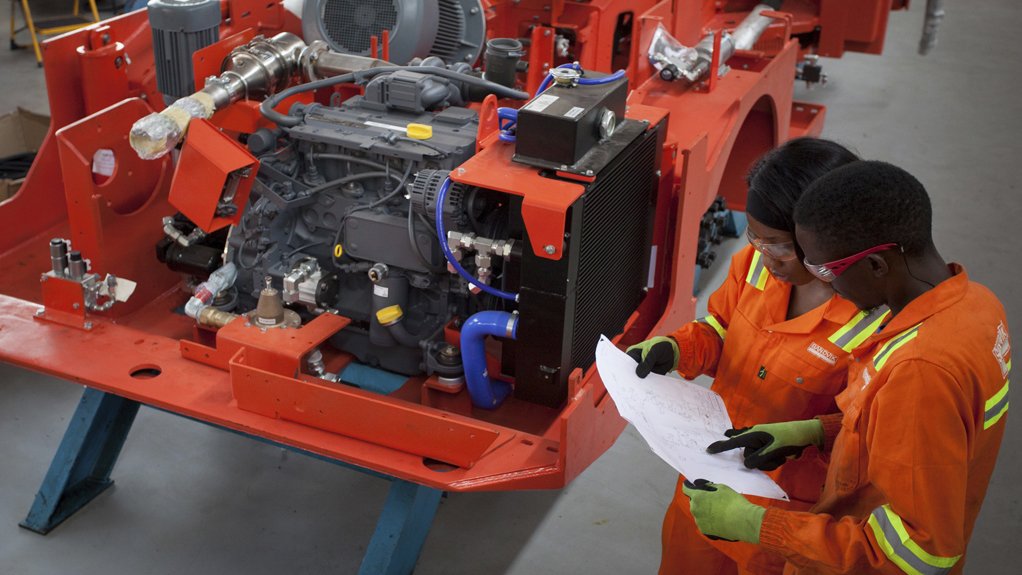
CRUSHERS, SCREENS AND FEEDERS The Sandvik Zimbabwe operation provides support for Sandvik Rock Processing’s range of crushers, screens and feeders
COMPLETE OVERHAUL The Sandvik operations in Zimbabwe have also evolved their support strategies to include a full remanufacturing service for its underground equipment
The modest size of Zimbabwe’s mining sector has not prevented Sandvik’s operation in the country from rolling out partnerships to enhance modern mining practices, with a highlight being an ongoing automation project where five automated trucks are deployed at an underground room-and-pillar mine, explains Sandvik Zimbabwe territory manager Brian Chitenderu.
This collaboration enabled an ambitious project to start a few years ago, in which a progressive mining customer partnered with Sandvik to introduce automation into a low profile, room-and- pillar environment.
The trials focused on testing 45 t Toro TH545i underground dump trucks in certain main haulages of the mine.
Among the factors to consider were that the mine runs mainly manual trackless equipment, which must interact with the automated units. The process required constant collaboration between the customer and various expert teams from Sandvik Mining and Rock Solutions.
Earlier this year, an important milestone was achieved with a fully automated loop that includes an underground crusher, he says.
“The automation project has been particularly exciting for us, as this has demonstrated how we can push boundaries with Sandvik’s leading edge digital technology. At the heart of technological progress like this are the strong relationships of trust that we have built with customers over many years,” says Chitenderu.
“The years leading up to this point saw a great deal of research and development work from our Finland factory, especially regarding the traffic management system,” he says, adding that this complex system manages five of the existing TH545i trucks, to which another five may still be added.
The success of these trials, notes Chitenderu, makes this intervention the first automated trucking loop in a low-profile, room-and-pillar environment.
“The next step in this phased automation approach will be to have a matching loader, and then go through the various stages of automation for the drills.”
Improved In-Country Support
Chitenderu highlights that the Sandvik operations in Zimbabwe have also evolved their support strategies to include a full remanufacturing service for its underground equipment, thereby offering expertise that goes beyond repairs or refurbishment, providing customers with cost-effective truck, loader or drill remanufacturing services in-country.
“The advantage of this model is that we can make a complete original equipment manufacturer’s assessment of what work needs to be done, and then return the machine to our stringent specifications,” he explains, adding that this enables Sandvik Zimbabwe to provide the machines it remanufactures the same warranty as a new unit, as the company knows the standard to which it has been rebuilt.
In the seven years that the remanufacturing programme has been active, 136 items of equipment have been remanufactured and returned to customers.
Among the infrastructure now supporting this effort is a rock drill testing facility, installed in November 2023.
“This automated testing unit allows us to assess each of the drills we work on, giving customers the confidence in the standards to which we operate,” he says, adding that Sandvik Zimbabwe also offers customers a range of support packages, from expertise-on-site to full maintenance contracts.
In addition to supporting the offerings that fall under the Sandvik Mining and Rock Solutions business area, the Zimbabwe operation also serves Sandvik Rock Processing’s range of crushers, screens and feeders.
“With our first dedicated employee already in place for Sandvik Rock Processing, we are developing the local capability for scheduled maintenance and breakdowns,” he says, adding that this is a key aspect of growing the company’s crushing and screening business in Zimbabwe.
Skills Upliftment
Skills development is a cornerstone of the company’s growth strategy, not just in terms of trainee numbers, but in the fast-changing nature of the expertise required.
In this regard, Chitenderu says the company’s apprenticeship programme has been evolving to include more electronics in the traditionally mechanical content, leading to training that is more focused on mechatronics and data analysis.
“We have even developed a new qualification and curriculum in collaboration with the national ministry of education, which will be available at technical colleges,” he says.
Sandvik’s pipeline of skills includes its own apprentices as well as graduate engineers, and the company is working with the University of Zimbabwe’s Engineering, Mining and Metallurgy Faculty, and the Zimbabwe School of Mines, to sensitise students in how technology is changing the mining sector.
“We are making future engineers aware of the digitalisation and automation journey currently underway in mining,” he says, adding that it is important that they are familiar with these trends when they enter the market after their studies.
Underpinning its service levels to customers in Zimbabwe is the ready availability of spare parts, concludes Chitenderu.
These are offered through over-the-counter sales and also through vendor-managed inventory or consignment stock, depending on what suits each customer.
Comments
Press Office
Announcements
What's On
Subscribe to improve your user experience...
Option 1 (equivalent of R125 a month):
Receive a weekly copy of Creamer Media's Engineering News & Mining Weekly magazine
(print copy for those in South Africa and e-magazine for those outside of South Africa)
Receive daily email newsletters
Access to full search results
Access archive of magazine back copies
Access to Projects in Progress
Access to ONE Research Report of your choice in PDF format
Option 2 (equivalent of R375 a month):
All benefits from Option 1
PLUS
Access to Creamer Media's Research Channel Africa for ALL Research Reports, in PDF format, on various industrial and mining sectors
including Electricity; Water; Energy Transition; Hydrogen; Roads, Rail and Ports; Coal; Gold; Platinum; Battery Metals; etc.
Already a subscriber?
Forgotten your password?
Receive weekly copy of Creamer Media's Engineering News & Mining Weekly magazine (print copy for those in South Africa and e-magazine for those outside of South Africa)
➕
Recieve daily email newsletters
➕
Access to full search results
➕
Access archive of magazine back copies
➕
Access to Projects in Progress
➕
Access to ONE Research Report of your choice in PDF format
RESEARCH CHANNEL AFRICA
R4500 (equivalent of R375 a month)
SUBSCRIBEAll benefits from Option 1
➕
Access to Creamer Media's Research Channel Africa for ALL Research Reports on various industrial and mining sectors, in PDF format, including on:
Electricity
➕
Water
➕
Energy Transition
➕
Hydrogen
➕
Roads, Rail and Ports
➕
Coal
➕
Gold
➕
Platinum
➕
Battery Metals
➕
etc.
Receive all benefits from Option 1 or Option 2 delivered to numerous people at your company
➕
Multiple User names and Passwords for simultaneous log-ins
➕
Intranet integration access to all in your organisation