Consultative approach critical for heavy-duty applications
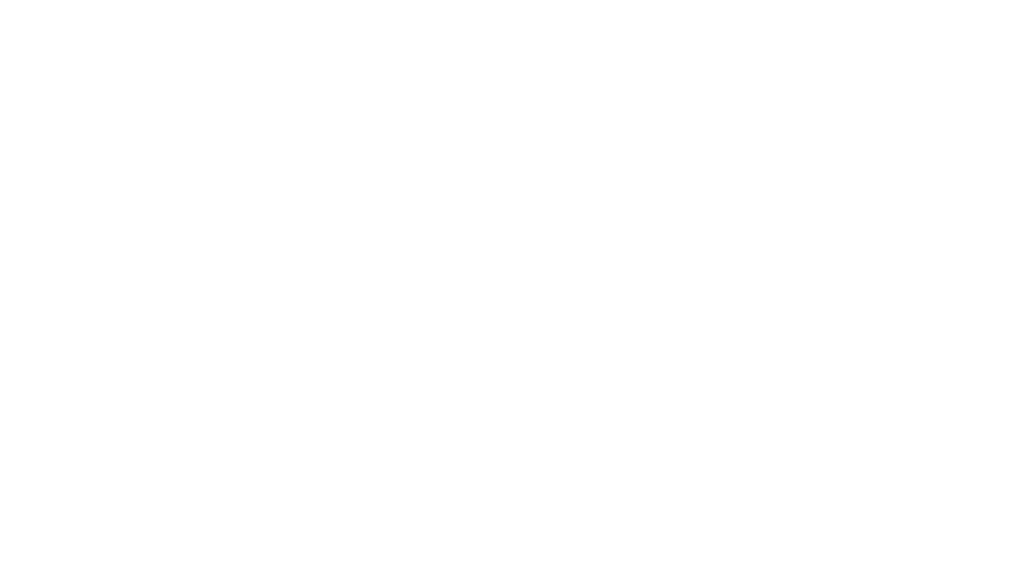
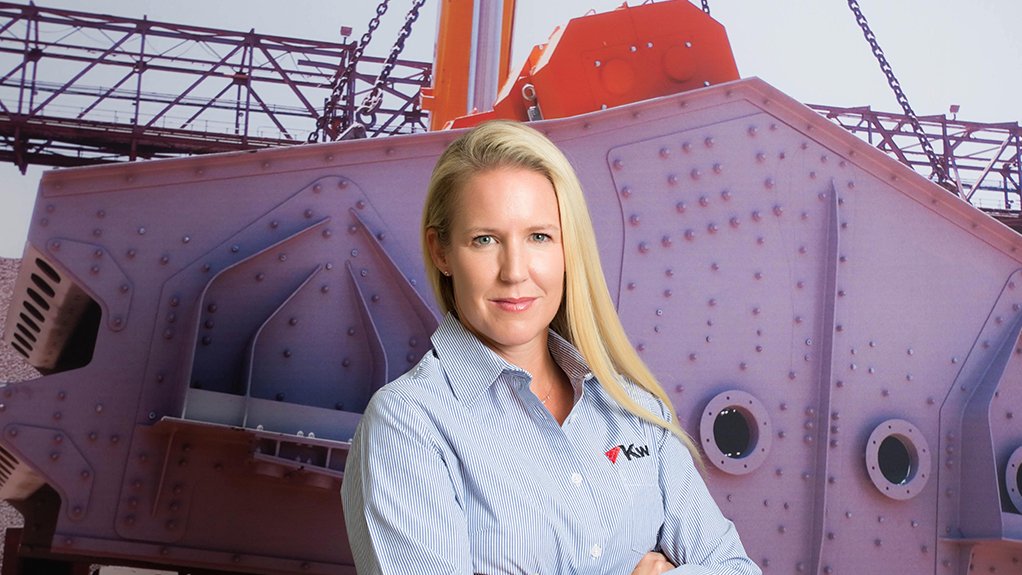
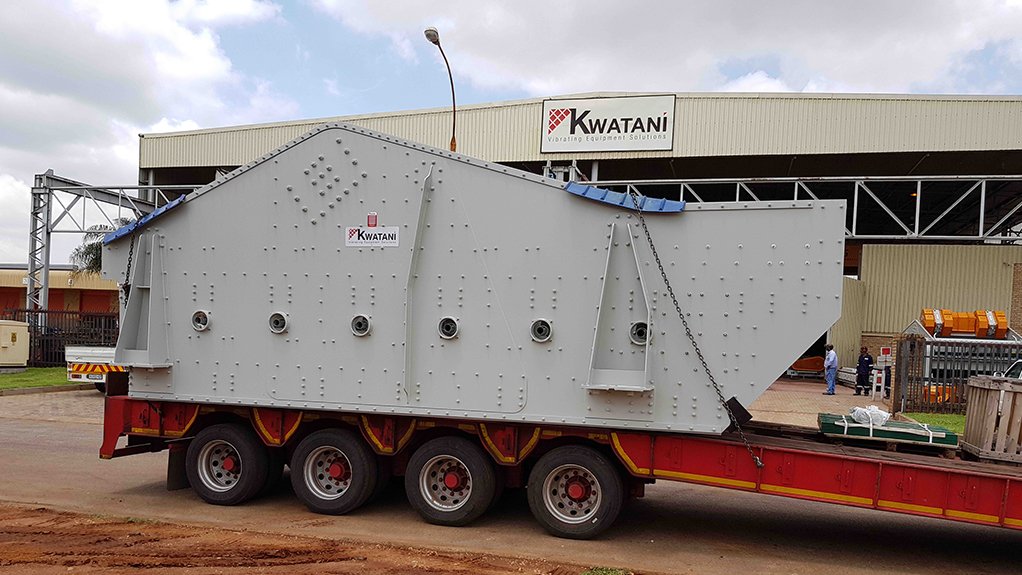
KIM SCHOEPFLIN By establishing a relationship with a customer, Kwatani is better equipped to customise vibrating equipment solutions
EN ROUTE A Kwatani manganese screen on its way to a customer
Considering that manganese, a base metal, is an abrasive material and demanding on equipment, industrial and mining vibrating screens manufacturer Kwatani CEO Kim Schoepflin highlights the importance of “getting to know the ore and the application”.
Consequently, a “consultative approach” is critical, she says, especially amid tight deadlines, pricing and advising customers.
Schoepflin comments that, by establishing a relationship with a customer, Kwatani is better equipped to customise vibrating equipment solutions, which subsequently lowers the total cost of ownership. The vibrating screens, she notes, form “a vital part of the process flow sheet” of a mining operation.
This is especially important when dealing with the harshness of a manganese application because Kwatani, an original-equipment manufacturer (OEM), develops suitable machinery for not just the ore and tonnage throughput, “but to meet the application’s duty”, adds Schoepflin.
Kwatani’s solutions are not “off the shelf”, providing the OEM with the added advantage of being able to fine- tune all screening parameters – whether it be the screening media, or the speed, the deck angle, the stroke and even the direction of the stroke of the machine – to find “the sweet spot” for efficiency and to meet all the requirements for an application.
“We focus on meeting the design criteria, specifically on being robust to ensure long life and continuous uptimes,” she says, explaining that the equipment’s longevity and its ability to “do what it’s supposed to do” significantly contributes to a lower cost of ownership.
“Kwatani’s equipment is engineered to last which is evident in our customers not being required to carry stock of any manufactured steel components,” Schoepflin adds.
The vibrating equipment’s design secures not only the efficiency that a mine wants to achieve but also the tonnage to achieve performance.
These large vibrating screens are driven by Kwatani’s heavy duty mechanical gearboxes, which provide the required G-forces to handle the significant production tonnages. Kwatani gearboxes are manufactured in-house, and are considered to be robust and reliable, even under the harshest operating conditions.
“We run each exciter gearbox at full load for one hour in our testing facility to ensure both our stringent in-house and ISO 9001-2015 standards are met,” Schoepflin says.
Each gearbox is designed and manufactured in-house and all parts, except for the bearings, are sourced from local suppliers in close proximity to Kwatani. This gives Kwatani a “big advantage”, as it provides the OEM with the ability to control the design and quality, and it speaks to localisation.
Kwatani also has its own metallurgical laboratory through which the company tests challenging applications and is able to make any amendments to the screening parameters on its wet and dry test screen and other vibrating equipment in pursuit of continuously delivering on its quality commitment. It also facilitates research and development initiatives with various universities.
Prior to dispatch, all units endure intensive testing at Kwatani’s facility, in Kempton Park, before being commissioned at a customer’s site. Testing protocols have been developed in-house and are performed under close engineering supervision.
Further, Kwatani is also committed to upholding quality standards in terms of its employees.
About half of the company’s workforce comprises tertiary-qualified engineers and artisans. “We believe in training and developing our staff to ensure that the quality of the customised unit meets the specifications”.
In terms of efficiency, Kwatani is able retrofit its vibrating equipment on the current equipment plant footprint, without requiring costly changes to existing plant infrastructure , says Schoepflin.
“This approach will generally provide improved plant performance and efficiency at the lowest cost of ownership”.
The rationale behind retrofitting is that, just as a mine changes tonnage throughput over time, so can its processes. Without changes to equipment, mines often have to deal with inefficient processes .
Retrofitting is one of Kwatani’s key factors of growth, Schoepflin says, adding that, in resolving these challenges, a mine’s efficiency increases.
On Route to Bigger Things
Kwatani has a very large equipment footprint across base metals processing plants, especially in challenging environments.
The company currently has an order on route to West Africa, which Schoepflin says “is bigger than the zinc/manganese project in the Northern Cape”.
Most recently, Kwatani supplied four heavy duty vibrating screens and ten feeders to a manganese operation, in the Northern Cape, to assist in boosting throughput, as part of the plant’s expansion.
The units supplied include a 3.6 m double-deck sizing screen, a 3 m double-deck washing screen, a 2.4 m double-deck washing screen and a 1.8 m dewatering screen and ten vibrating feeders.
While Kwatani has a strong presence locally, Schoepflin notes that, given South Africa’s current economic environment, as well as the challenges in local mining and manufacturing, it is “important to continue local manufacturing while looking outside the country’s borders for additional growth”.
However, Schoepflin tells Mining Weekly that exporting alone is not the long-term strategy to disperse its machines globally. As such, Kwatani has agents worldwide and is considering setting up in strategic locations.
“We’re testing the waters with partners where we’re going to perhaps develop a more comprehensive relationship than what we would have with an agency”.
Kwatani recently exported to its fortieth country and is currently located in the large mining jurisdictions in North and South America.
Comments
Press Office
Announcements
What's On
Subscribe to improve your user experience...
Option 1 (equivalent of R125 a month):
Receive a weekly copy of Creamer Media's Engineering News & Mining Weekly magazine
(print copy for those in South Africa and e-magazine for those outside of South Africa)
Receive daily email newsletters
Access to full search results
Access archive of magazine back copies
Access to Projects in Progress
Access to ONE Research Report of your choice in PDF format
Option 2 (equivalent of R375 a month):
All benefits from Option 1
PLUS
Access to Creamer Media's Research Channel Africa for ALL Research Reports, in PDF format, on various industrial and mining sectors
including Electricity; Water; Energy Transition; Hydrogen; Roads, Rail and Ports; Coal; Gold; Platinum; Battery Metals; etc.
Already a subscriber?
Forgotten your password?
Receive weekly copy of Creamer Media's Engineering News & Mining Weekly magazine (print copy for those in South Africa and e-magazine for those outside of South Africa)
➕
Recieve daily email newsletters
➕
Access to full search results
➕
Access archive of magazine back copies
➕
Access to Projects in Progress
➕
Access to ONE Research Report of your choice in PDF format
RESEARCH CHANNEL AFRICA
R4500 (equivalent of R375 a month)
SUBSCRIBEAll benefits from Option 1
➕
Access to Creamer Media's Research Channel Africa for ALL Research Reports on various industrial and mining sectors, in PDF format, including on:
Electricity
➕
Water
➕
Energy Transition
➕
Hydrogen
➕
Roads, Rail and Ports
➕
Coal
➕
Gold
➕
Platinum
➕
Battery Metals
➕
etc.
Receive all benefits from Option 1 or Option 2 delivered to numerous people at your company
➕
Multiple User names and Passwords for simultaneous log-ins
➕
Intranet integration access to all in your organisation