Flexible girth-gear drive systems for Mpumalanga mill
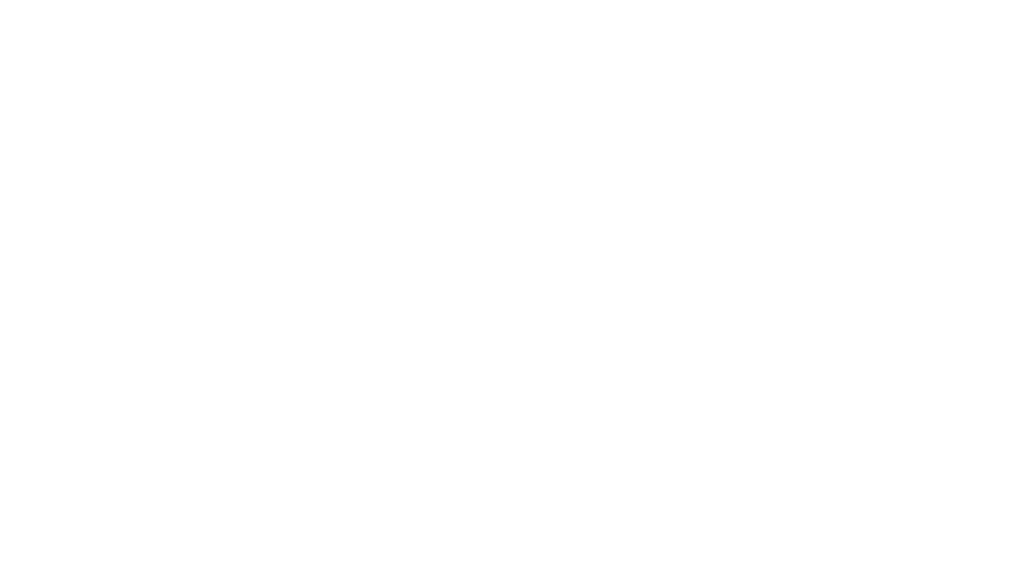
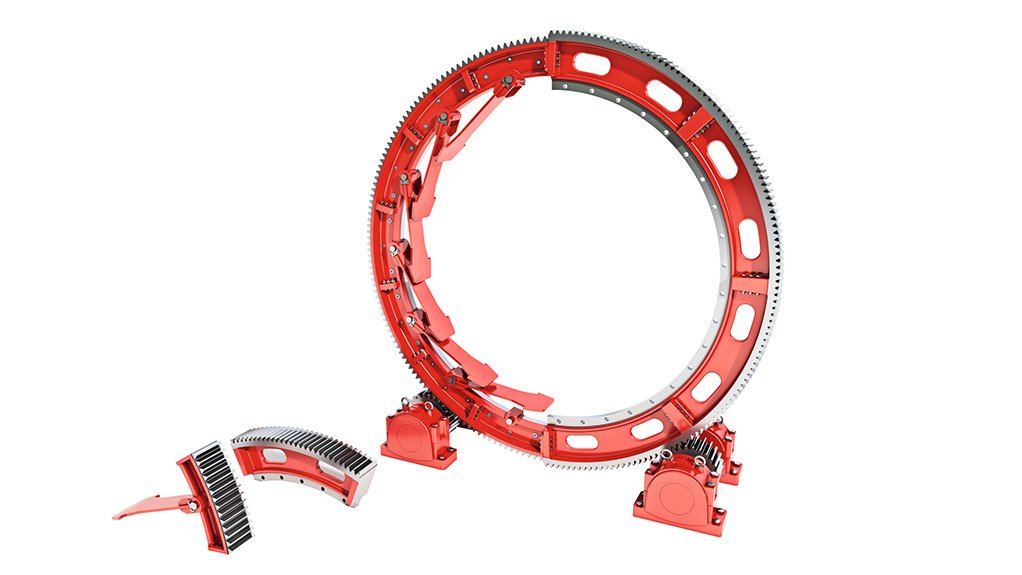
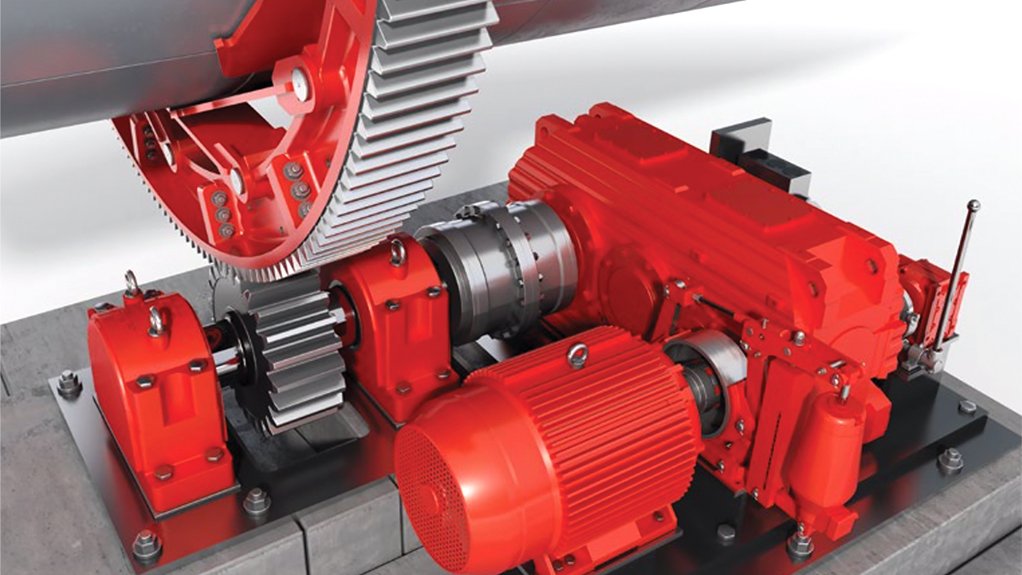
SEGMENTED SEW-Eurodrive’s segmented girth gear solution relies on precision manufacturing of individual segments
SEW-Eurodrive supplied a total drive solution to go with the segmented girth gears
Drive technology company SEW-Eurodrive has delivered four of its modern industrial girth gear drive systems to a mine in Limpopo for the refurbishment of the rotary scrubber.
The order for four 5.3-m-diameter girth gear drive systems, coupled with the X2FS220 drive system, was issued in mid-2020, with the client requesting a rapid turnaround. The full system and all components were delivered to site in December 2020. The first gear set was installed in September last year by a crew of 20 people including SEW-Eurodrive engineers and subcontractor technicians. The remaining units are to be installed one at a time at various intervals expected later this year.
“Installation is being deliberately staggered to accommodate the scheduled maintenance shutdowns at the facility. We are in constant communication with the mine to do the changeovers, with a view to avoiding disruption to production and unnecessary downtime,” SEW-Eurodrive project engineer Bruce Farthing tells Engineering News.
“Now that our crew is familiar with the mine and the installation requirements, the remaining three installations shouldn’t take more than a couple of weeks from shutdown to commissioning,” Farthing assures.
SEW-Eurodrive’s segmented girth gear solution relies on precision manufacturing of individual segments to simplify handling, transportation and onsite assembly of these very large open gears.
“Flexibility is key. This solution allows us to ship and deliver the whole system to site in standard containers, while also simplifying onsite assembly,” he adds.
Describing how traditional open girth gears are manufactured, he says that castings are first made in two or four segments. The segments are then assembled into a ring for machining using huge and expensive geargrinding equipment. After machining, the open gear wheel is again split into its segments for heat treatment, finishing and shipping. All complete girth sets typically consists of ten segments and upwards.
“The size of each traditional girth gear, however, makes casting and heat treatment very difficult, which often results in quality issues,” Farthing adds. A set of segmented girth gears reduces this issue.
He notes that the industrial girth gears the company supplied to the mine in Limpopo were each shipped to site in 10 identical segments for easy assembling on site. This can be done far more quickly and with much less lifting equipment, he says. An added advantage of segmented girth gears is the ability to stock and replace an individual segment in the event of a breakdown to keep a mill or kiln turning while a new complete girth gear is manufactured.
“This kind of manufacturing design also allows us to ship large girth gears in smaller modular formats,” he adds.
On the material side, SEW-Eurodrive uses austempered ductile iron (ADI) for the production of its girth gears.
“ADI is produced using a modern tempering process, which is a heat treatment procedure that requires precisely controlled temperatures. This results in cast iron with a refined grain structure that gives more toughness and less hardness than traditional girth gear materials,” he says.
The Total Mill Drive Solution
While the girth gears are key final-stage components of the mill drives and rotary scrubbers, SEW-Eurodrive supplied a total drive solution for these systems. “For each of these girth gear systems, we also supplied large two-stage industrial gearboxes (IGs) and the external pinions to drive the girth gear, which were also designed and manufactured by SEW-Eurodrive,” says Farthing, adding that the motors are coupled to the gearboxes using a fluid coupling on a purpose-built, drop-in baseplate.
Smaller gearboxes from SEW-Eurodrive’s X series range are also coupled to the main gearbox as auxiliary drives for commissioning and maintenance purposes.
Condition Monitoring
For continuous condition monitoring, the mine requested an oil-monitoring capability on all of the industrial gearboxes, Farthing says.
“Built-in sensors continuously monitor oil pressure and temperature to ensure healthy lubrication. The system automatically transmits a warning to the control room in the event of a low-pressure value, so that the drive systems can be immediately shut down to identify the problem,” he explains.
A kidney-loop oil filtration system for gearboxes also manages lubricant integrity. Any wear metal particles, water droplets or other contaminants in the oil are filtered out to extend lubricant life and prevent accelerated gearbox wear.
Temperature sensors also monitor bearing and oil temperatures. These sensors also act as an early warning system to ensure that potential problems are pre-emptively resolved. They also assist with scheduling oil change intervals.
Farthing notes that the value of the order, comprising four segmented girth gears, four associated drive train solutions and the auxiliary equipment, is competitively priced – not to mention the competitive lead times for completing the order.
“Ordering all four units upfront, even if not installed immediately, mitigates against delays that might have occurred as a result of components being shipped from SEW-Eurodrive’s overseas manufacturing facilities.
For girth-gear solutions and all of the company’s total drive solutions’ offerings, Farthing says SEW-Eurodrive believes in consulting extensively with its clients so that system design engineers, installers and plant operators can collectively come up with effective, economical and reliable solutions.
Comments
Press Office
Announcements
What's On
Subscribe to improve your user experience...
Option 1 (equivalent of R125 a month):
Receive a weekly copy of Creamer Media's Engineering News & Mining Weekly magazine
(print copy for those in South Africa and e-magazine for those outside of South Africa)
Receive daily email newsletters
Access to full search results
Access archive of magazine back copies
Access to Projects in Progress
Access to ONE Research Report of your choice in PDF format
Option 2 (equivalent of R375 a month):
All benefits from Option 1
PLUS
Access to Creamer Media's Research Channel Africa for ALL Research Reports, in PDF format, on various industrial and mining sectors
including Electricity; Water; Energy Transition; Hydrogen; Roads, Rail and Ports; Coal; Gold; Platinum; Battery Metals; etc.
Already a subscriber?
Forgotten your password?
Receive weekly copy of Creamer Media's Engineering News & Mining Weekly magazine (print copy for those in South Africa and e-magazine for those outside of South Africa)
➕
Recieve daily email newsletters
➕
Access to full search results
➕
Access archive of magazine back copies
➕
Access to Projects in Progress
➕
Access to ONE Research Report of your choice in PDF format
RESEARCH CHANNEL AFRICA
R4500 (equivalent of R375 a month)
SUBSCRIBEAll benefits from Option 1
➕
Access to Creamer Media's Research Channel Africa for ALL Research Reports on various industrial and mining sectors, in PDF format, including on:
Electricity
➕
Water
➕
Energy Transition
➕
Hydrogen
➕
Roads, Rail and Ports
➕
Coal
➕
Gold
➕
Platinum
➕
Battery Metals
➕
etc.
Receive all benefits from Option 1 or Option 2 delivered to numerous people at your company
➕
Multiple User names and Passwords for simultaneous log-ins
➕
Intranet integration access to all in your organisation