Global green alloy acclaim is there for South Africa to attain using new local technology
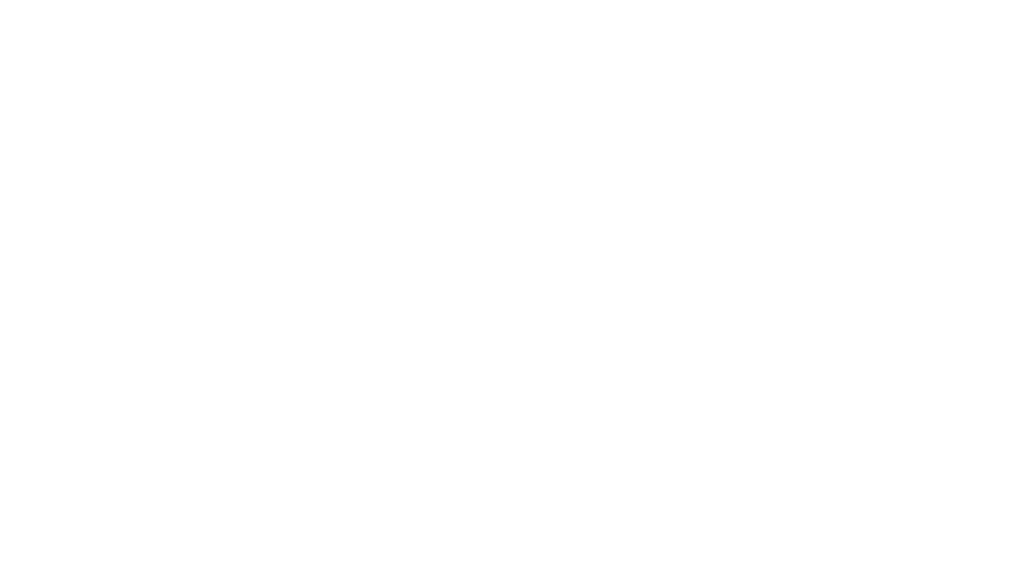
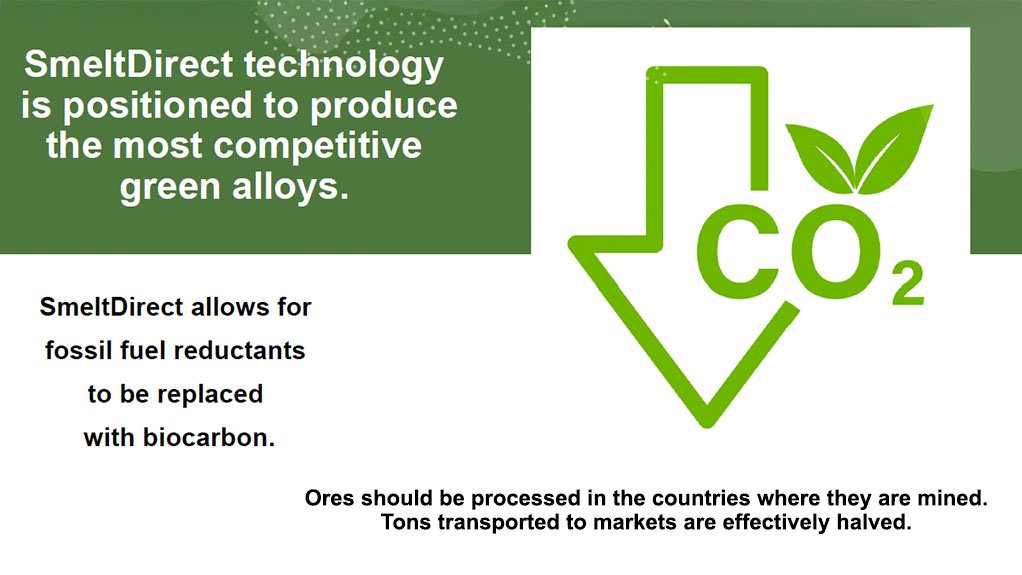
South African technology positioned to elevate alloy production to new high level of greenness.
JOHANNESBURG (miningweekly.com) – South Africa, which hosts more than 70% of the world reserves of chrome ore and manganese ores, was dominant in ferroalloy production until 2010.
In the early 2000s, South Africa was the undisputed No 1 chrome ore- and ferrochrome-producing country, with 90% of the inputs, including technology and equipment, locally sourced.
More than 200 000 direct and indirect jobs were created across the chrome value chain and 20% of mining-related foreign exchange was earned from ferrochrome sales.
In 2010, the chrome value chain contributed R42-billion to South Africa’s GDP and generated R36-billion worth of foreign exchange earnings, with ferrochrome production contributing 80% of the value of the chrome value chain.
Even then, South Africa’s closed furnaces reduced CO2 emissions and increased energy efficiency. It was only soaring public-sector power tariffs that caused the industry to lose its grip on the global market.
But now, new South African technology is positioned to take greenness and cleanness to a high new level at a time when the likes of Carbon Border Adjustment Mechanism (CBAM) imposition are only a little over a year away, in a world in which combatting climate change is an essential requirement.
SmeltDirect, which has been tried, tested and proven, will be on the receiving end of value from CBAM carbon credits, giving South Africa an open window of opportunity to regain lost ground with bottom-of-the-cost-curve competitiveness.
Hugely advantageous for South Africa’s stumbling ferroalloy industry is the development of a new technology by the Johannesburg Stock Exchange-listed African Rainbow Minerals headed by executive chairperson Dr Patrice Motsepe, which has no intention of holding it close to their chests.
Instead, ARM Ferrous division CE Andre Joubert, and ARM executive technology development Henk Bouwer, are determined to do what is best for the country and that is to spread the patented SmeltDirect as far and as wide as possible by retrofitting it to the considerable number of dormant smelters so that restarts get under way without delay.
Importantly, the technology is positioned to produce the most competitive green alloy, which is just what the world needs.
Advantageously, SmeltDirect not only has all the attributes to reverse South Africa’s downward ferrochrome and ferromanganese slide but could even bring back the likes of Highveld Steel and Vanadium as well as open the way for a return of the local production of high-manganese rail.
A detailed bankable feasibility study has been completed, engagement with ferroalloy peers on joint venture partnerships has taken place, and funding and co-financing arrangements for what will be a major generator of direct and indirect jobs are showing early promise. Some 700 jobs are created for every 200 000 t of alloy production a year and South Africa was once a producer of about four- or five-million tons a year, which points to the potential of creating tens of thousands of new jobs.
Moreover, the use of renewable energy with biocarbon can slash Scope 1 and 2 carbon emissions by up to 80% and Scope 3 emissions are halved.
Major logistical cost- and emission-reduction benefits result from ores being processed in the countries where they are mined.
No reasonable competitive entity anywhere in the world could justifiably aver that it is not correct for South Africa, which hosts overwhelming volumes of raw ore to process as much raw ore as possible close to where it is mined.
South Africa is by no means a newcomer to local alloy, which is clearly illustrated by this country being one of the originators of the International Ferro-Alloy Conference, where ferroalloy smelting knowledge is discussed.
Currently, however, conventional smelting of ferrochrome and ferromanganese are seen as no longer having a sound future in South Africa and the prevailing viewpoint is that more income can be generated by exporting the ores rather than adding any local value to them.
The production of manganese alloys such as ferromanganese, silicomanganese and medium carbon ferromanganese is said to be on the way out and the remaining smelters are targeting lower electricity price agreements.
In addition to over-the-top electricity price increase, changes that have knocked the bottom out of South Africa’s alloy competitiveness have been the placing of higher emphasis on exporting ore to alloy competitors outside of the country rather than local beneficiation.
Also, although ferrochrome is a key ingredient of stainless steel production emphasis was not placed on substantially increasing local stainless steel production.
Now, the need for greenness to combat climate change and the emergence of new low-cost and competitive smelting regime must be grasped as part of a united national effort.
Fortunately, South Africa is entering a new era of public-private collaboration, which is targeting economic growth that is inclusive.
A new minerals energy momentum must be generated to fulfil the sustainability requirements of a world that has no option but to implement environment-friendly outcomes.
What must not be ignored is that SmeltDirect uses 70% less electricity, cuts costs meaningfully, slashes emissions and can make good use of the lowest of low-grade input materials.
Only 1.2 MW of electricity is needed to produce a ton of alloy, unlike the 4 MW required by conventional systems, and some 700 jobs are created for every 200 000 t of alloy production a year.
At one stage, installed ferrochrome capacity alone was 4.8-million tons. Getting back to that competitively will be of substantial benefit to the South African economy and should be implemented as part of a public-private programme.
Comments
Press Office
Announcements
What's On
Subscribe to improve your user experience...
Option 1 (equivalent of R125 a month):
Receive a weekly copy of Creamer Media's Engineering News & Mining Weekly magazine
(print copy for those in South Africa and e-magazine for those outside of South Africa)
Receive daily email newsletters
Access to full search results
Access archive of magazine back copies
Access to Projects in Progress
Access to ONE Research Report of your choice in PDF format
Option 2 (equivalent of R375 a month):
All benefits from Option 1
PLUS
Access to Creamer Media's Research Channel Africa for ALL Research Reports, in PDF format, on various industrial and mining sectors
including Electricity; Water; Energy Transition; Hydrogen; Roads, Rail and Ports; Coal; Gold; Platinum; Battery Metals; etc.
Already a subscriber?
Forgotten your password?
Receive weekly copy of Creamer Media's Engineering News & Mining Weekly magazine (print copy for those in South Africa and e-magazine for those outside of South Africa)
➕
Recieve daily email newsletters
➕
Access to full search results
➕
Access archive of magazine back copies
➕
Access to Projects in Progress
➕
Access to ONE Research Report of your choice in PDF format
RESEARCH CHANNEL AFRICA
R4500 (equivalent of R375 a month)
SUBSCRIBEAll benefits from Option 1
➕
Access to Creamer Media's Research Channel Africa for ALL Research Reports on various industrial and mining sectors, in PDF format, including on:
Electricity
➕
Water
➕
Energy Transition
➕
Hydrogen
➕
Roads, Rail and Ports
➕
Coal
➕
Gold
➕
Platinum
➕
Battery Metals
➕
etc.
Receive all benefits from Option 1 or Option 2 delivered to numerous people at your company
➕
Multiple User names and Passwords for simultaneous log-ins
➕
Intranet integration access to all in your organisation