Facilities equipped for custom orders
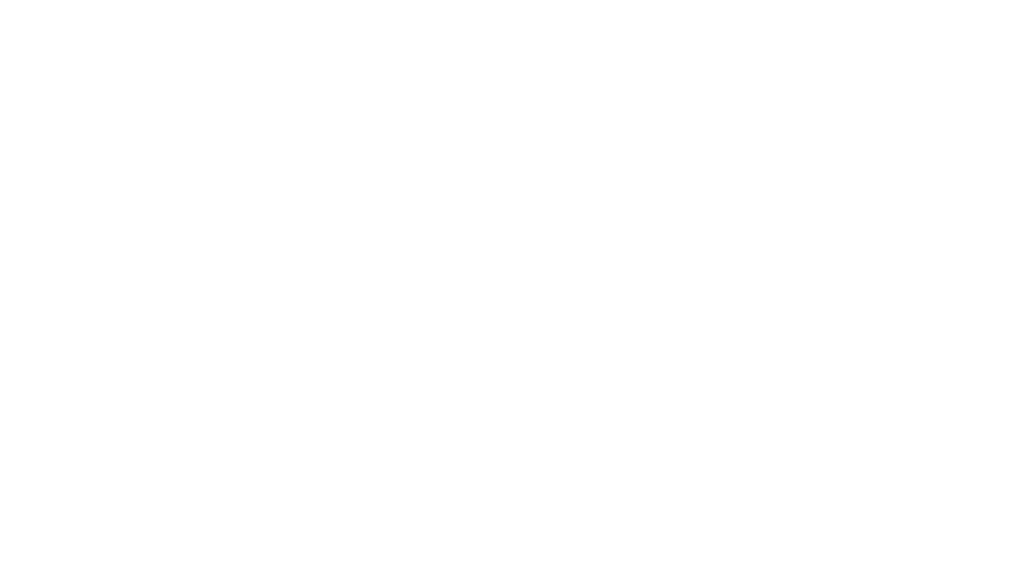
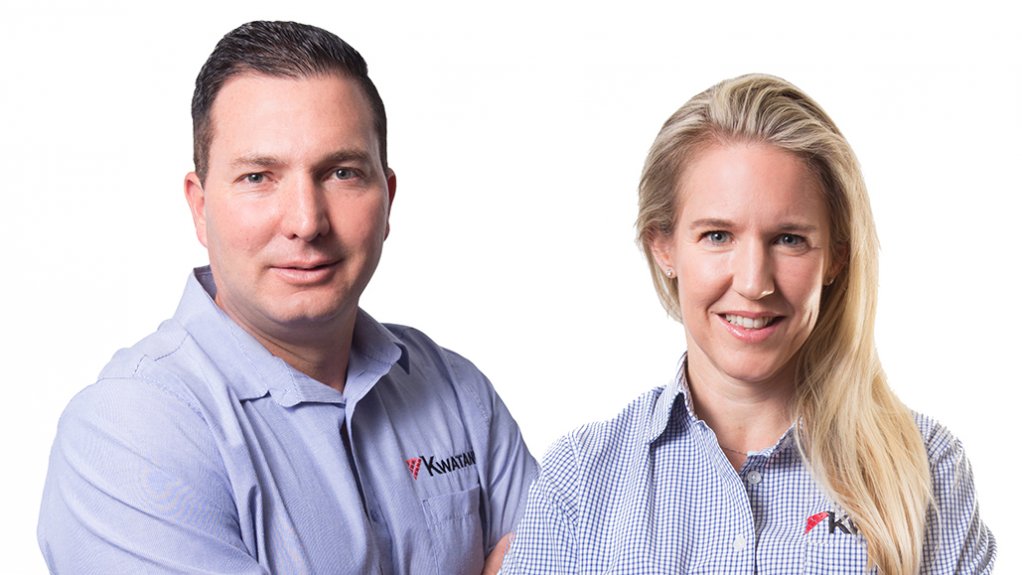
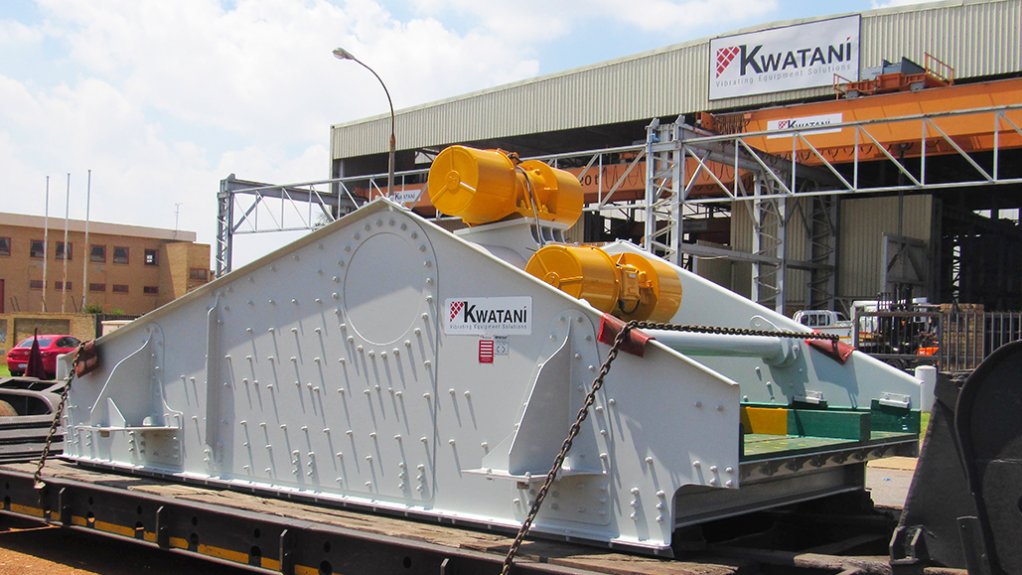
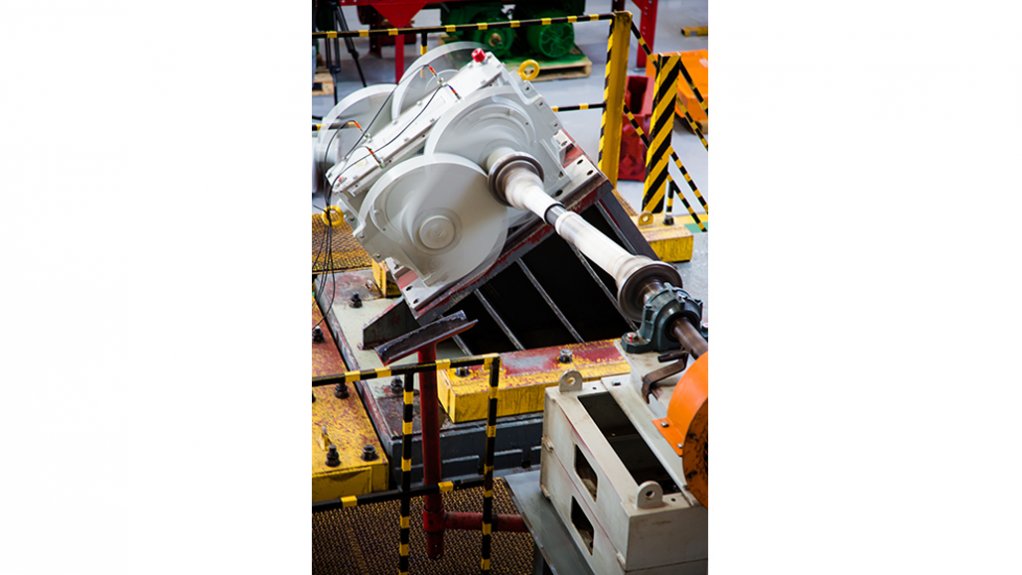
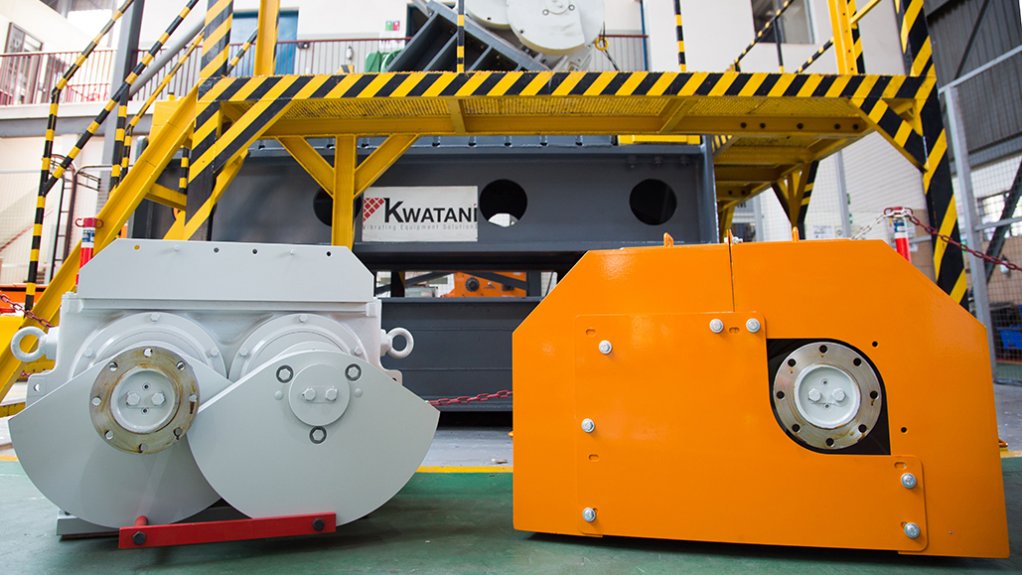
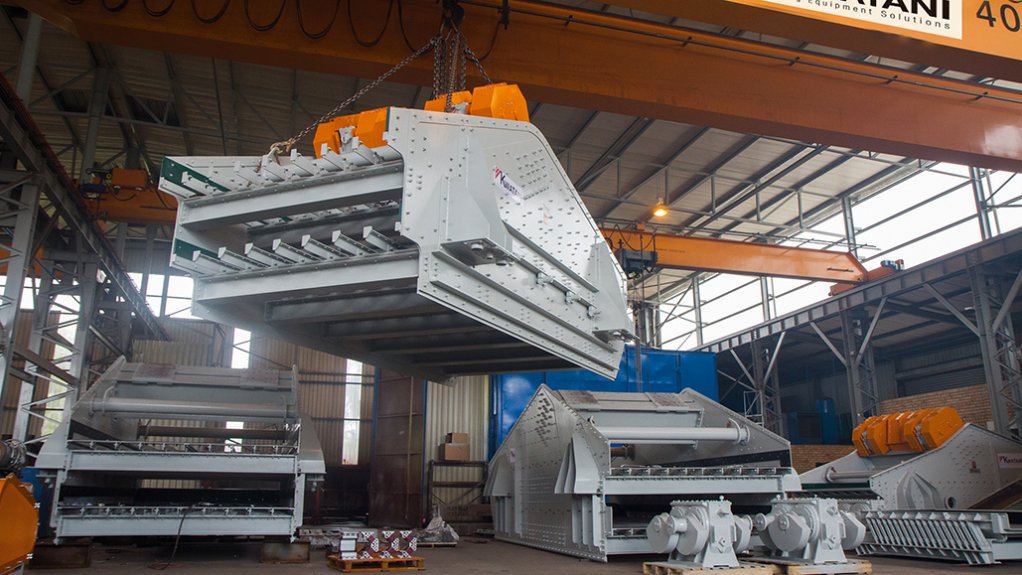
RIAAN STEINMANN, KIM SCHOEPFLIN Operations GM at Kwatani, and CEO, respectively
CUSTOM-DESIGNED VIBRATING EQUIPMENT One of many single deck screens manufactured by Kwatani ready for delivery
EXTENSIVE TESTING A Kwatani exciter being tested on the test bench in the drives department
VITAL ROLE IN MACHINE DESIGNS A covered and uncovered exciter with the test bench in the background in the drives workshop at Kwatani
PRECISION-ENGINEERED JIGS Screens being moved with ease by the overhead cranes operational at Kwatani
Original-equipment manufacturer (OEM) Kwatani’s fabrication jobbing processes are designed to deliver custom-designed vibrating equipment within timeframes similar to those of other OEMs that deliver standard equipment.
“Our processes are based on a job-based system, so the entire production facility layout is arranged in a job-process environment, where all processes are highly streamlined,” explains Kwatani CEO Kim Schoepflin.
Kwatani’s 17 000 m2 facility in Kempton Park, Johannesburg, includes its head office; facilities for engineering, manufacturing, assembly, separate stainless steel welding, the manufacturing and repair of exciter gearboxes and electrical motor assembly; testing, laboratory and refurbishment facilities; and a warehouse.
The facilities are designed to ensure swift responsiveness and can handle large-scale, multiple machine projects while ensuring flexibility to support customers that want to place emergency orders.
Kwatani engineers vibrating equipment, such as vibrating screens and feeders, to meet specific application requirements of clients.
Schoepflin claims that each step of the manufacturing process for custom-designed vibrating equipment is specialised in different aspects of fabrication such as boilermaking, welding, assembling and factory acceptance testing of machines.
“We’re able to divide highly customised machines into its components which are fabricated in different work stations, where we work through some of the components so that we have the same production speed as in a batch production system.”
Schoepflin stresses that Kwatani continuously invests in its own facilities, with recent investments upgrading its final product testing facilities in which machines are tested before dispatch as well as ongoing improvements to various work stations located throughout the fabrication process.
The facilities also include a material testing laboratory equipped with a wide range of testing equipment, such as a versatile vibrating test screen, to conduct material testing. This unit can adjust parameters such as drive angle, deck angle, stoke, speed and screen media to determine the optimal screening parameters for difficult to screen material received from customers before the design process begins.
In addition to a material testing laboratory, Kwatani also has a testing station that is used for testing its exciter gearboxes at full load prior to dispatch to the customer.
“We’ve also invested in a larger test floor and resources to make sure that we can test numerous vibrating machines in quick succession. We will invest further in this area, as we are increasing the number of screening machines that we produce, which is currently about one machine a day, after being tested.”
The 100 m2 factory test floor is also equipped with 380 V and 525 V variable-speed drive controllers to accommodate site- specific voltage drive requirements.
Kwatani has also invested in condition monitoring to complement its testing facilities to ensure that it can always compare its factory-acceptance tests to those that are conducted at clients’ sites where its vibrating equipment is used.
Kwatani operations GM Riaan Steinmann highlights the importance of the quality hold points Kwatani implements to ensure that “quality is built into the fabrication process”.
These quality hold points are implemented as several inspections to ensure that the quality of fabricated components is maintained, particularly as these components are moved through the
different steps of the fabrication process.The quality hold points also ensure that the necessary measurements of components are taken, and that potential errors are identified and corrected.
“When clients request a custom-built machine from Kwatani, they are also able to check or add additional hold points throughout the process,” says Schoepflin.
Quality control starts from the beginning, at the client interface, and ends with ongoing service, she declares.
“Our metallurgical engineers consult with the clients to ensure they fully understand their expectations in terms of the material, application, related up- and downstream processes, plant footprint and desired outcome, and this is considered up to the mechanical engineering phase and procurement of the machines,” she points out.
Steinmann adds that check sheets are also completed at quality hold points, which are also used to form a data book for the Kwatani products, containing relevant information from the quality checks. These data books are supplied to the customer.
“If there is a quality issue, we always investigate the underlying root cause. This ensures not only that the product or component is correct but also that we try to align our processes and learn from them for continuous improvement,” enthuses Schoepflin.
Comments
Press Office
Announcements
What's On
Subscribe to improve your user experience...
Option 1 (equivalent of R125 a month):
Receive a weekly copy of Creamer Media's Engineering News & Mining Weekly magazine
(print copy for those in South Africa and e-magazine for those outside of South Africa)
Receive daily email newsletters
Access to full search results
Access archive of magazine back copies
Access to Projects in Progress
Access to ONE Research Report of your choice in PDF format
Option 2 (equivalent of R375 a month):
All benefits from Option 1
PLUS
Access to Creamer Media's Research Channel Africa for ALL Research Reports, in PDF format, on various industrial and mining sectors
including Electricity; Water; Energy Transition; Hydrogen; Roads, Rail and Ports; Coal; Gold; Platinum; Battery Metals; etc.
Already a subscriber?
Forgotten your password?
Receive weekly copy of Creamer Media's Engineering News & Mining Weekly magazine (print copy for those in South Africa and e-magazine for those outside of South Africa)
➕
Recieve daily email newsletters
➕
Access to full search results
➕
Access archive of magazine back copies
➕
Access to Projects in Progress
➕
Access to ONE Research Report of your choice in PDF format
RESEARCH CHANNEL AFRICA
R4500 (equivalent of R375 a month)
SUBSCRIBEAll benefits from Option 1
➕
Access to Creamer Media's Research Channel Africa for ALL Research Reports on various industrial and mining sectors, in PDF format, including on:
Electricity
➕
Water
➕
Energy Transition
➕
Hydrogen
➕
Roads, Rail and Ports
➕
Coal
➕
Gold
➕
Platinum
➕
Battery Metals
➕
etc.
Receive all benefits from Option 1 or Option 2 delivered to numerous people at your company
➕
Multiple User names and Passwords for simultaneous log-ins
➕
Intranet integration access to all in your organisation