Right culture takes safety performance to next level
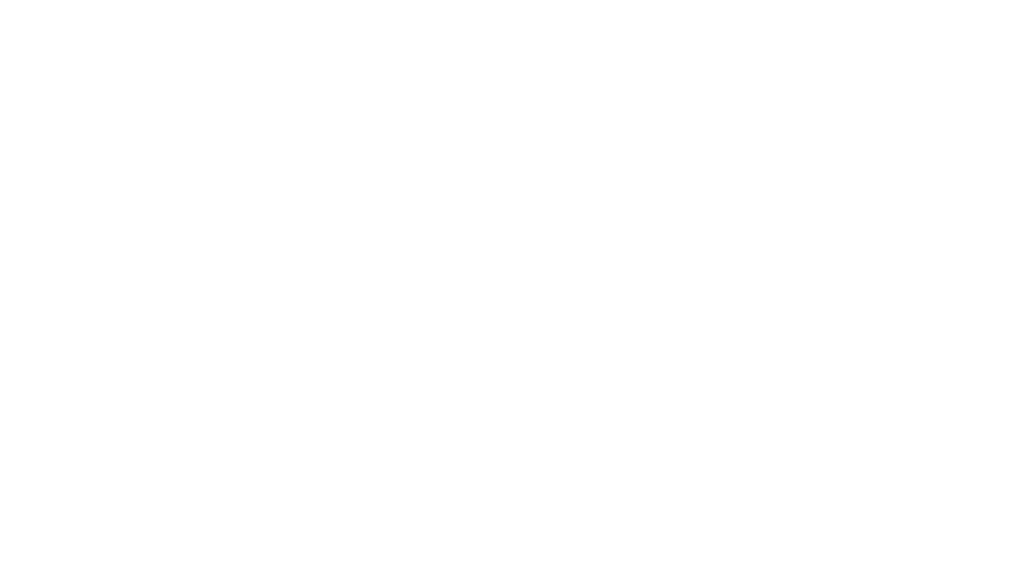
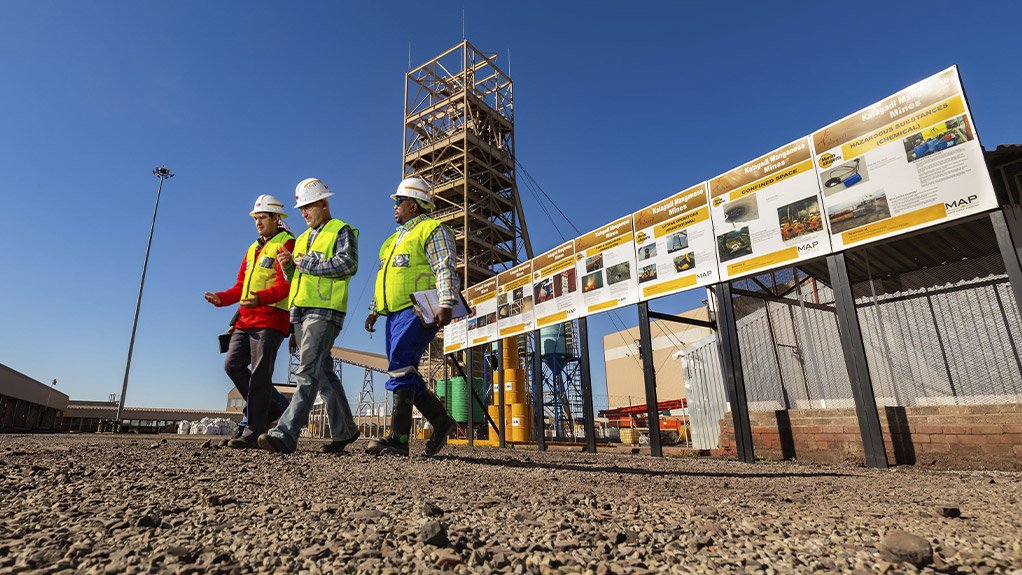
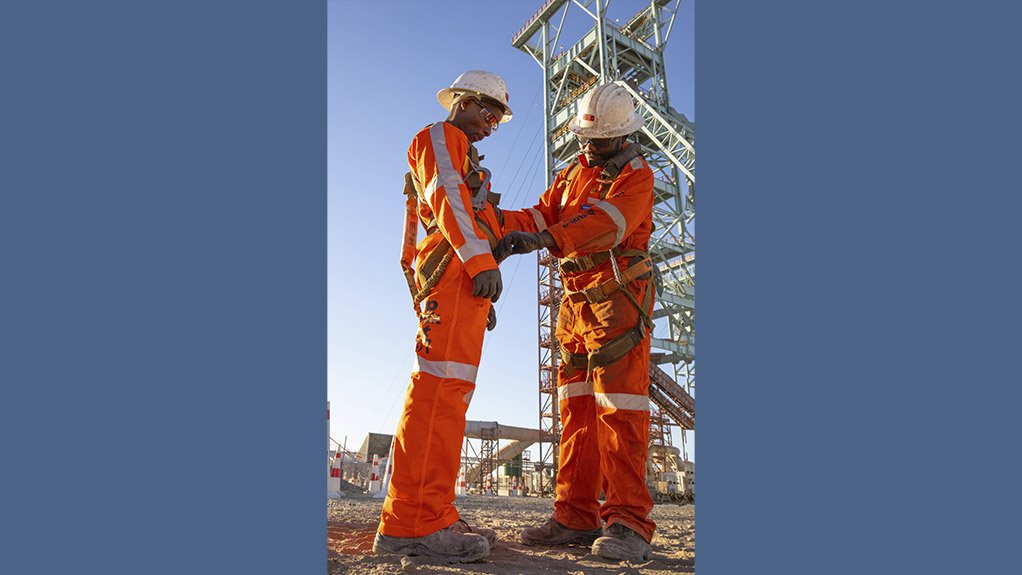
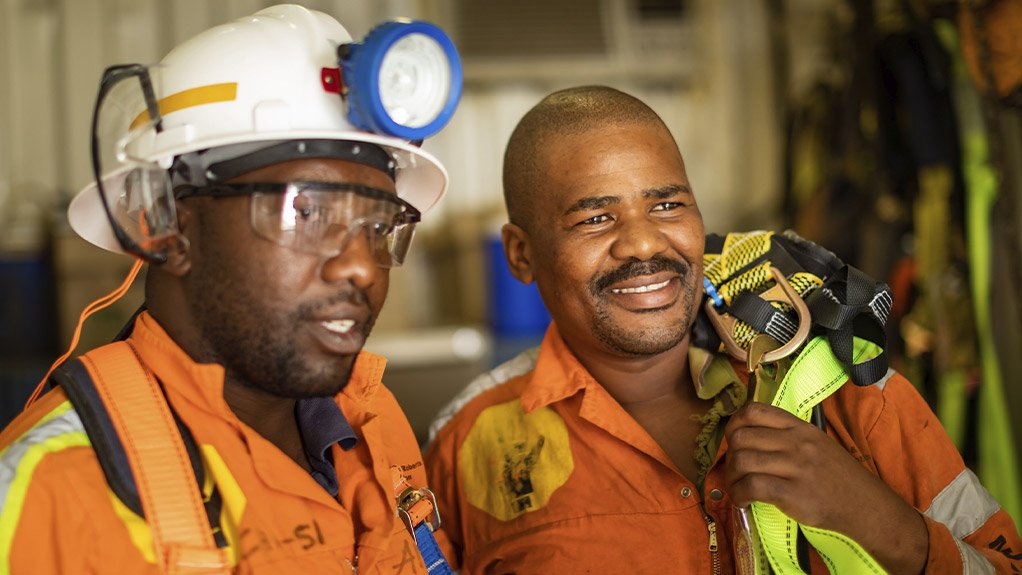
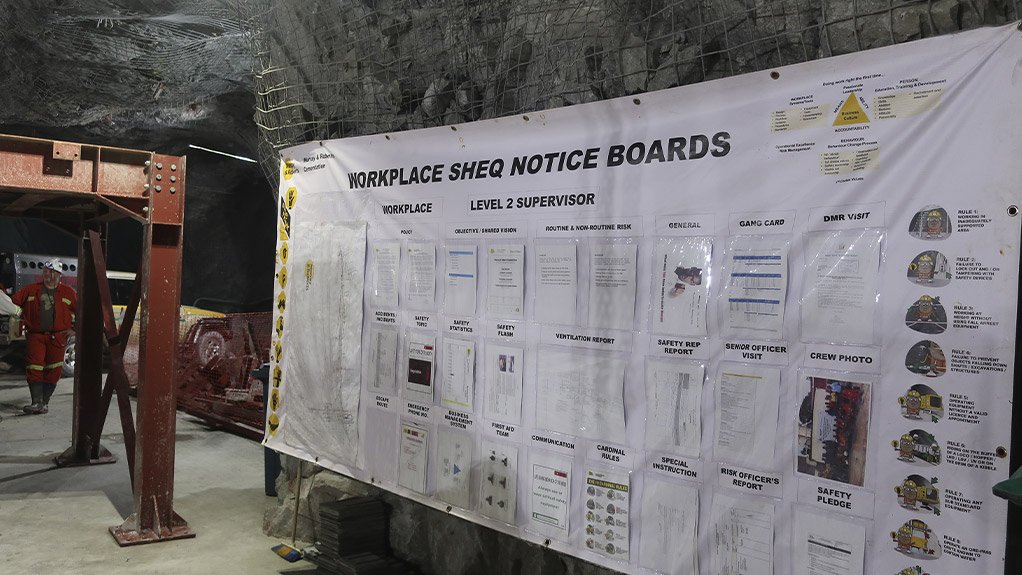
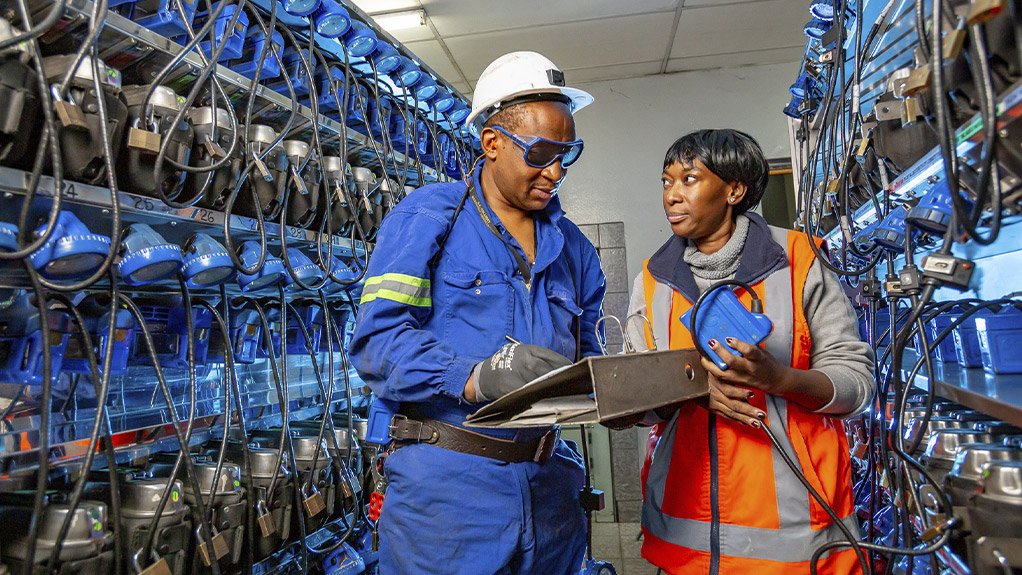
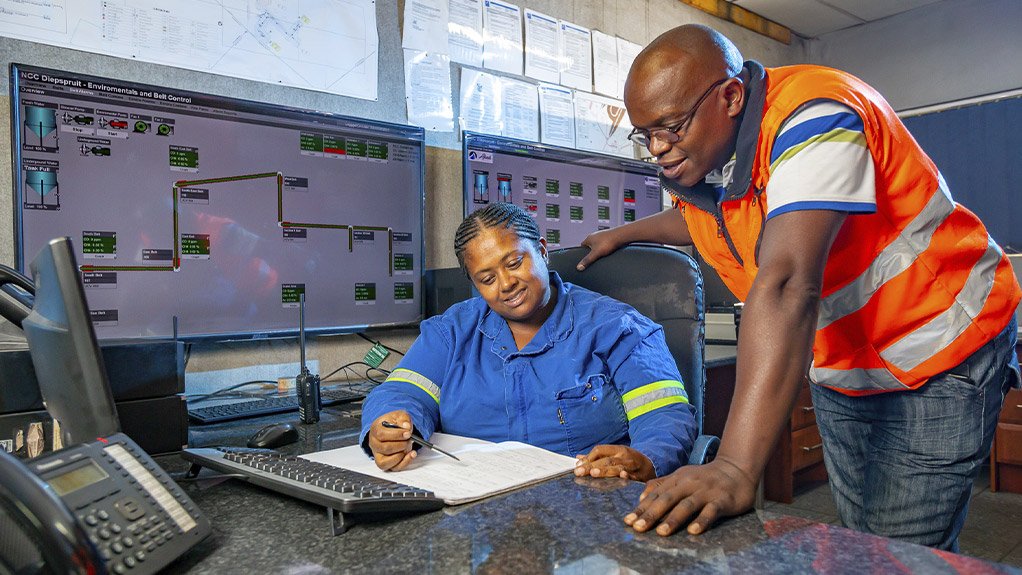
It is the culture of the workplace that has made at the difference when it comes to safety at Murray & Roberts Cementation
Murray & Roberts Cementation has fostered a culture of safety among its people
Appreciating employees not just for their work but also for their minds and hearts drives safe behaviour at Murray & Roberts Cementation
Comprehensive checks and balances are in place which ensure a safe working culture at Murray & Roberts Cementation
Underpinning the Murray & Roberts Cementation safety culture are the standards and systems which remain an important foundation
Murray & Roberts Cementation reinforces a caring culture through daily integration between management and staff
This article has been supplied.
In the mining sector’s ongoing quest for zero harm, Murray & Roberts Cementation has shown that a culture of safety is critical to meeting this target – over and above the progress made in safety systems and technologies.
In its own safety journey, the company has made great strides, according to Trevor Schultz, Risk Executive at Murray & Roberts Cementation. Among the key indicators of its success is that it has been fatality-free for almost a decade, a real accolade in the traditionally high-risk field of shaft sinking and mine development.
“It has been a journey that started long before 2015, when we reviewed the systems and processes, customising them to suit our business needs,” says Schultz. “Working closely with our Training Academy at Bentley Park, we also developed a new approach that would foster a culture of safety among our people – from their very first days in training.”
The Training Academy prepares employees to perform their work in the most efficient and safe manner, he says, including tailor-made programmes for mining and engineering supervisors.
“We believe that to create the right business culture, we need to give employees the means and ability to do their work – and after that you can hold them accountable to do the work right,” he explains. “Our programmes include License to Supervise, as well as Risk Management, to ensure alignment of our safety principles across the business.”
This approach has also achieved a steady decrease in the company’s Lost Time Injury rate. Graham Chamberlain, Murray & Roberts Cementation’s New Business Executive, concurs that the safety culture has been critical to these gains.
“An important shift in the mining sector has been to appreciate employees not only for their hands (to work) and their ears (to listen), but for their minds and hearts – which really drive safe behaviour,” says Chamberlain. “Systems and rules are important, but they don’t provide the vocabulary to show that management really cares about the safety of every employee.”
A caring culture is reinforced every day by the interaction between management and staff, he argues. This forms part of the company’s Visible Felt Leadership initiative, which ensures managers engage with their teams on a regular basis.
Underpinning the safety culture are the standards and systems, which remain an important foundation for safety at Murray & Roberts Cementation, says Schultz.
“We have a robust health, safety and environment (HSE) framework which covers key points such as systems, standards and internal and external audits,” he says. “We also have formalised strategies to learn from incidents on site – both within the company and externally – and we share best practice and learning across our regions.”
Comprehensive checks and balances are in place, including self-assessments for supervisors and managers, which help to determine the effectiveness of training in the workplace. Benchmarking against the highest standards, Murray & Roberts Cementation is certified in terms of ISO 9000, ISO 14000 and ISO 45000 in its internal systems and corporate governance.
Technology also has a role to play in supporting the safety culture, explains Chamberlain, especially in removing people from the ‘contact area’ where most safety hazards are found.
“We work to engineer the risk out of every working situation, which usually involves the use of equipment instead of manual labour,” he explains. “Equally, the solution may be to revise the methodology or the working cycle – as this affects the way the employee behaves.”
He notes that operating under excessive pressure, or experiencing undue frustration in their work, will have an impact on an individual’s safety performance. Part of the safety effort, therefore, is to alleviate these factors and improve the working environment – which in turn leads to the right behaviours.
Schultz points to a range of engineering technologies that Murray & Roberts Cementation has adapted and applied to improve safety. Lasers have been employed to continuously monitor clearances in some vertical shaft projects, so that winder speeds can be reduced where the clearance reaches limitations.
“We have extended the pre-sink automated tipping hook and kibble auto alignment to the main sink which removes the human interaction during tipping,” he continues. “The monitoring of our stage zone kibble winder slack rope has also been updated, by allowing continued monitoring during crosshead arresting. Electrical actuators are now being used where possible, instead of the noisier air and hydraulic system.”
Murray & Roberts Cementation is also an early adopter of technology that can improve safety, such as Proximity Detection Systems (PDS). In the early 2000s, the company saw the value of this emerging field of electronics, and was one of the first local companies to trial it on its trackless mining machinery.
“We were able to prove the efficacy of this technology, and quickly progressed to standardise PDS as a minimum requirement on our machines,” he says. “This was years before it was made mandatory, which required all qualifying mines to install this equipment.”
The safety approach has even affected the kinds of projects and tasks that Murray & Roberts Cementation will take on, he explains.
“By reviewing our projects’ safety performance, we identified certain categories of work as being very high-risk,” he says. “The decision was made that if the risk of harm cannot be reduced to an acceptable level – through mechanising, automation or safer methods – then we would simply not undertake such work.”
Comments
Press Office
Announcements
What's On
Subscribe to improve your user experience...
Option 1 (equivalent of R125 a month):
Receive a weekly copy of Creamer Media's Engineering News & Mining Weekly magazine
(print copy for those in South Africa and e-magazine for those outside of South Africa)
Receive daily email newsletters
Access to full search results
Access archive of magazine back copies
Access to Projects in Progress
Access to ONE Research Report of your choice in PDF format
Option 2 (equivalent of R375 a month):
All benefits from Option 1
PLUS
Access to Creamer Media's Research Channel Africa for ALL Research Reports, in PDF format, on various industrial and mining sectors
including Electricity; Water; Energy Transition; Hydrogen; Roads, Rail and Ports; Coal; Gold; Platinum; Battery Metals; etc.
Already a subscriber?
Forgotten your password?
Receive weekly copy of Creamer Media's Engineering News & Mining Weekly magazine (print copy for those in South Africa and e-magazine for those outside of South Africa)
➕
Recieve daily email newsletters
➕
Access to full search results
➕
Access archive of magazine back copies
➕
Access to Projects in Progress
➕
Access to ONE Research Report of your choice in PDF format
RESEARCH CHANNEL AFRICA
R4500 (equivalent of R375 a month)
SUBSCRIBEAll benefits from Option 1
➕
Access to Creamer Media's Research Channel Africa for ALL Research Reports on various industrial and mining sectors, in PDF format, including on:
Electricity
➕
Water
➕
Energy Transition
➕
Hydrogen
➕
Roads, Rail and Ports
➕
Coal
➕
Gold
➕
Platinum
➕
Battery Metals
➕
etc.
Receive all benefits from Option 1 or Option 2 delivered to numerous people at your company
➕
Multiple User names and Passwords for simultaneous log-ins
➕
Intranet integration access to all in your organisation