Stationary hydrogen power highlighted as major solution by Toyota fuel cell-using developer
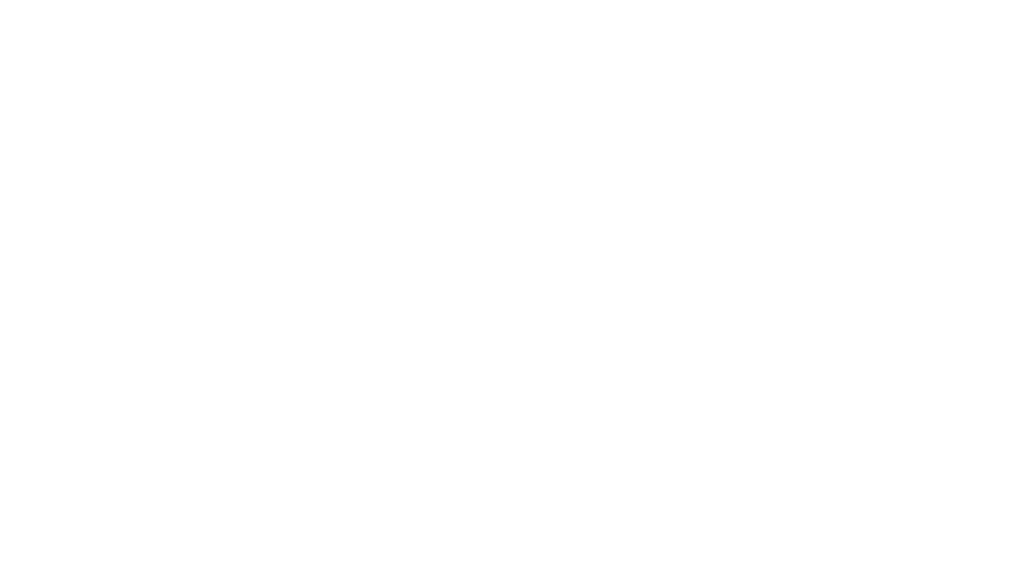

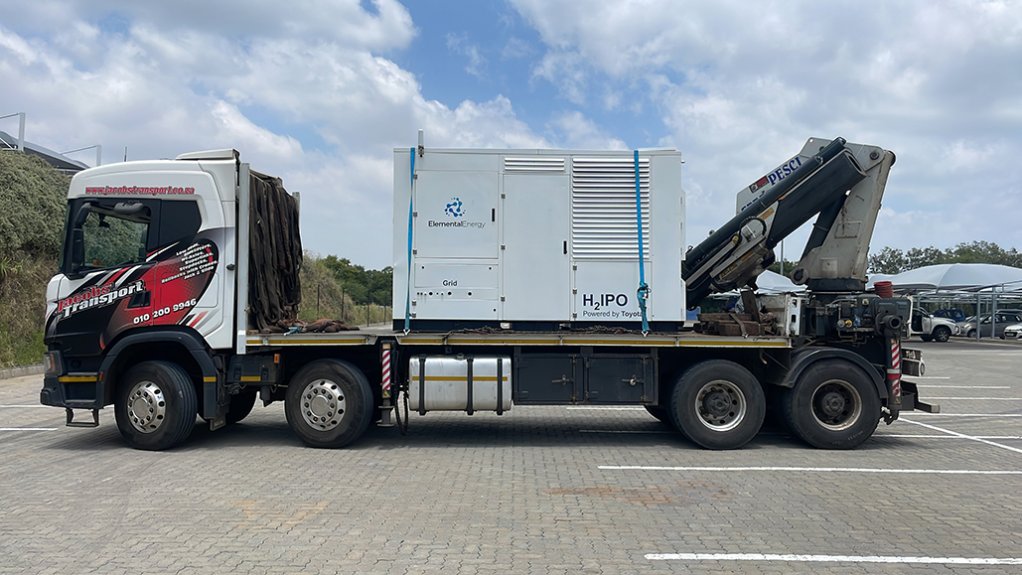
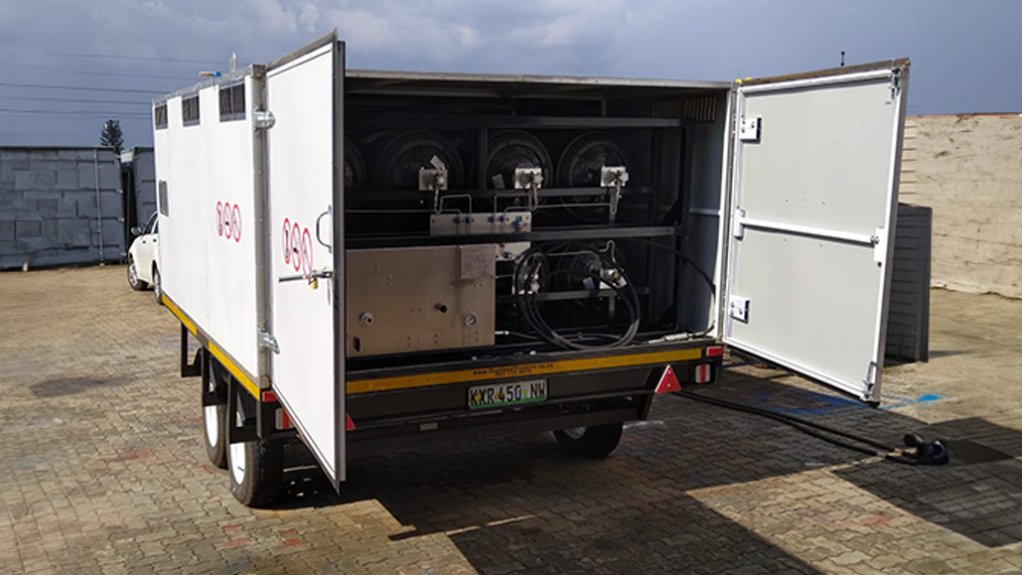
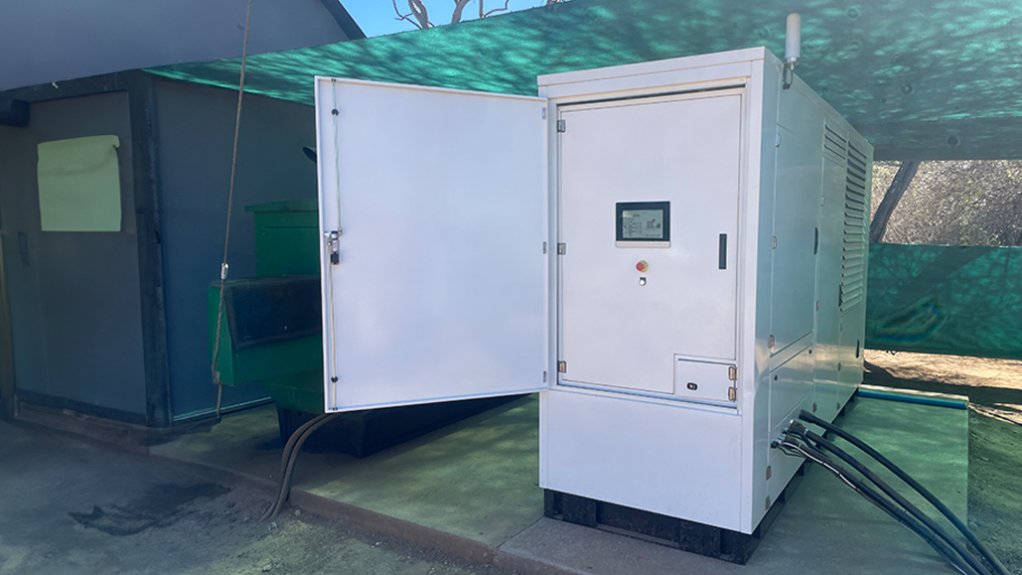
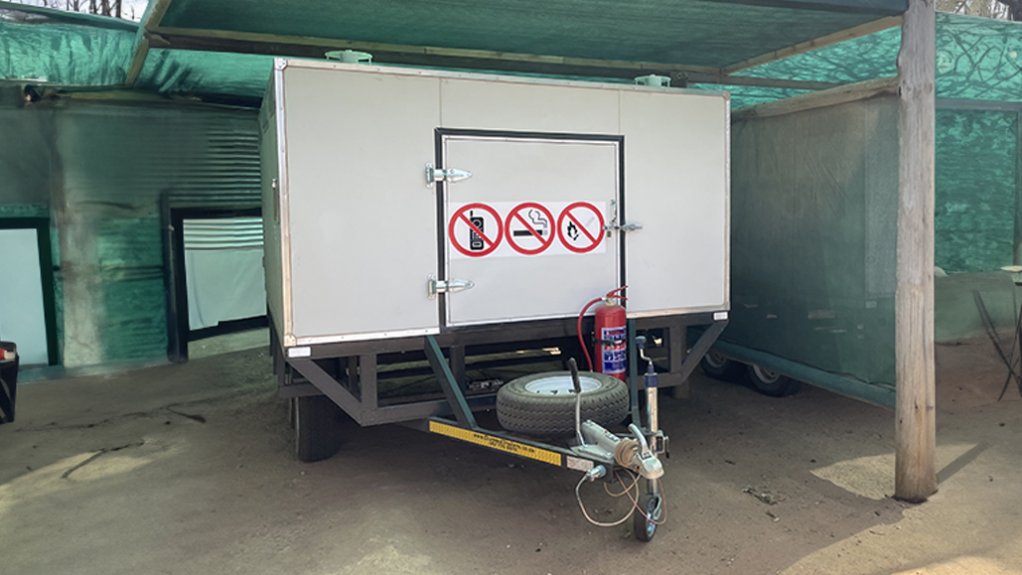
Elemental Energy’s Dereck Armstrong interviewed by Mining Weekly's Martin Creamer. Video: Darlene Creamer
Elemental Energy equipment.
Elemental Energy equipment
Elemental Energy equipment
Elemental Energy equipment
Elemental Energy equipment
JOHANNESBURG (miningweekly.com) – When Engineering News & Mining Weekly covered last month’s local launch of BMW’s first hydrogen car fleet on South Africa's roads, we discovered that BMW’s hydrogen refilling station in Midrand is powered by Elemental Energy’s off-grid hydrogen power system, which has a crucial Toyota fuel cell underpin.
Interestingly, we now learn that Elemental Energy is on a major mission to build hydrogen power systems in developing countries in particular.
“We are just at the beginning of seeing the many applications of green hydrogen play out globally, and we think stationary power is one of the most important to get right, especially in Africa,” Elemental Energy’s Dereck Armstrong told Mining Weekly in a note ahead of our Zoom interview on March 7. (Also watch attached Creamer Media video.)
Already operating in South Africa on grid, solar, battery and hydrogen is Elemental Energy's 100 kW system at Jaci’s Lodges in the Madikwe Game Reserve in North West province, a demonstrator that is already attracting considerable attention from the mining and agriculture sectors. The hydrogen for that site was produced on a nearby commercial farm and delivered in trailer units by Elemental Energy, which sees itself as an integrator of hydrogen technology that has Toyota’s automotive fuel cells in its power units.
“Toyota have been a great partner and deliver a truly high-performing and tested piece of kit,” said Armstrong, who views hydrogen supply for stationary power as the leading use case for developing green hydrogen supply in many regions.
This coincides with a comment made this week by the World Platinum Investment Council, which forecasts that stationary hydrogen fuel cells and hydrogen electrolysers will increase demand for platinum by more than 120% this year.
Toyota uses platinum-catalysed fuel cells and Elemental Energy is mulling the potential use of platinum-based proton exchange membrane (PEM) for some sites.
“Green hydrogen can already be produced at prices that compete with diesel on a dollar per kilowatt hour basis and it is only going to become more competitive over the next few years,” said Armstrong.
“We see hydrogen supply for stationary power being the leading use case for developing green hydrogen supply in many regions. With green hydrogen supply and demand coming online at the same time to replace diesel, the added benefit of a local supply is provided that can also be used to add vehicles or other hydrogen use cases as offtakers from the same infrastructure,” Armstrong said.
Adding storage capacity for hydrogen, a transportable renewable fuel, is relatively cheap and a fuel cell with gas storage can deliver long-duration energy.
“Our solution is actually an integrated solar/wind, battery and hydrogen system to deliver a cost-effective hybridisation of these technologies.
“We see ourselves as a technology integrator, which, when it comes to hydrogen, involves a fair bit of intellectual property and expertise itself.
“We work with some of the leading technology suppliers of electrolysis, compressors, hydrogen storage, batteries, inverters, and fuel cells and build the systems and controls to get all of these working together smoothly.
“Our core system is a smart power station that looks similar to a big diesel generator but is actually a lot more than that. It really becomes the brains and controls of all the power supply and storage on site.
“We also integrate hydrogen storage cylinders into a smaller trailer design that we build and assemble ourselves. This allows us to move hydrogen around quite efficiently for low distance, high frequency distribution.
“The hydrogen fuel cell does the job typically done by a diesel generator. The fuel cell chemically recombines hydrogen with oxygen to produce water, heat and electricity, so this is not a combustion process.
“Fuel cells are more efficient than combustion, they are also silent and with far less moving parts meaning the maintenance and life of the systems are significantly better.
“They also perform well at low power ranges. While diesel generator performance declines significantly as it goes below 50% of rated output, fuel cells maintain efficiency down to 10% of rated output. which means they are great to run at low rates to top up energy supply arising from solar or battery storage,” said Armstrong.
The heat that fuel cells produce can be transferred to geysers or to preheat a boiler feed.
“If the heat is captured and used properly, the conversion of the energy content from the hydrogen to useful energy is around a high 85% plus.
“With current green hydrogen costs, one can replace the role of diesel in an integrated energy system at energy costs 10% to 15% lower than diesel – and that’s taking into account the cost of capital and all the operating expenditure, but that excludes the use of heat. If you use the heat correctly, the system can be made to deliver energy at 25% lower cost per kilowatt hour than diesel generation.
“The main kicker here is that this is all very low carbon. Even the lifecycle emissions of the hardware are low. Electrolysers, storage cylinders and fuel cells use quite common metal and limited amounts of rare metals with significant associated carbon,” added Armstrong.
His goal for future projects is to build small hydrogen hubs where green hydrogen supply can be established for a cluster of customers to minimise the fuel costs and transport distances.
Mining Weekly: What sizes can these systems get to, is this viable for businesses, for industry, for grid energy supply?
Armstrong: We’ve built a 100 kW and 200 kW unit which was our starting point. We’re now developing our first 1 MW unit that can also synchronise and stack together for multi-megawatt sites. At multi-megawatt scales and with some technology development we see a role for hydrogen in supporting grids.
Like grid-connected batteries, adding electrolysis load to grids that run counter to peak grid demand and soak up excess renewable energy is a great way of supporting the addition of more renewables to our grids.
Do your systems consume a lot of water?
We do use hydrogen that has been produced by splitting water, but at the scales that we are using it in our projects at the megawatt level, the amounts of water used are typically a fraction of the total water consumed at a site we’re powering. Because we’re not exporting hydrogen, when the fuel cells reconstitute water, the condensate water that is produced is recovered at or near where it has been consumed, also reducing the total water impact of the project.
What about safety risks or concerns about the flammability of hydrogen?
Another common question, and understandably. The hydrogen systems we use are built to the highest standards meaning that every bit of hardware has been tested and certified to work with high-pressure hydrogen. As long as storage and use of hydrogen comply with proper regulations and standards, we see it as a similar risk level to working with any other flammable gas or fuel.
Comments
Press Office
Announcements
What's On
Subscribe to improve your user experience...
Option 1 (equivalent of R125 a month):
Receive a weekly copy of Creamer Media's Engineering News & Mining Weekly magazine
(print copy for those in South Africa and e-magazine for those outside of South Africa)
Receive daily email newsletters
Access to full search results
Access archive of magazine back copies
Access to Projects in Progress
Access to ONE Research Report of your choice in PDF format
Option 2 (equivalent of R375 a month):
All benefits from Option 1
PLUS
Access to Creamer Media's Research Channel Africa for ALL Research Reports, in PDF format, on various industrial and mining sectors
including Electricity; Water; Energy Transition; Hydrogen; Roads, Rail and Ports; Coal; Gold; Platinum; Battery Metals; etc.
Already a subscriber?
Forgotten your password?
Receive weekly copy of Creamer Media's Engineering News & Mining Weekly magazine (print copy for those in South Africa and e-magazine for those outside of South Africa)
➕
Recieve daily email newsletters
➕
Access to full search results
➕
Access archive of magazine back copies
➕
Access to Projects in Progress
➕
Access to ONE Research Report of your choice in PDF format
RESEARCH CHANNEL AFRICA
R4500 (equivalent of R375 a month)
SUBSCRIBEAll benefits from Option 1
➕
Access to Creamer Media's Research Channel Africa for ALL Research Reports on various industrial and mining sectors, in PDF format, including on:
Electricity
➕
Water
➕
Energy Transition
➕
Hydrogen
➕
Roads, Rail and Ports
➕
Coal
➕
Gold
➕
Platinum
➕
Battery Metals
➕
etc.
Receive all benefits from Option 1 or Option 2 delivered to numerous people at your company
➕
Multiple User names and Passwords for simultaneous log-ins
➕
Intranet integration access to all in your organisation